Integrated device for flue gas denitrification, deboration and dust removal in ultra-thin float glass substrate production line
A float glass and production line technology, applied in gas treatment, combined devices, separation methods, etc., can solve problems such as increasing the initial concentration of nitrogen oxides, and achieve the effect of reducing the amount of generation
- Summary
- Abstract
- Description
- Claims
- Application Information
AI Technical Summary
Problems solved by technology
Method used
Image
Examples
Embodiment Construction
[0038] like figure 1 As shown, the present invention provides an integrated device for flue gas denitration, deboron and dust removal in an ultra-thin float glass substrate production line, including:
[0039] a. Lime storage and transportation department,
[0040] combine figure 2 As shown, the lime storage and transportation part includes a slaked lime storage bin 12, and a first dust collector 11 is arranged on the top of the slaked lime storage bin 12; a first rotary valve 13 is provided at the bottom of the slaked lime storage bin 12, and the bottom of the first rotary valve 13 is from top to bottom. There is a weighing bin 14, a screw conveyor 15, a second rotary valve 16 and a gas-solid mixing bin 17 connected in sequence; the inlet of the gas-solid mixing bin 17 is respectively connected to the outlet of the conveying fan 18 and the second rotary valve 16;
[0041] b, heat exchange and cooling section,
[0042] combine image 3 As shown, the heat exchange and cool...
PUM
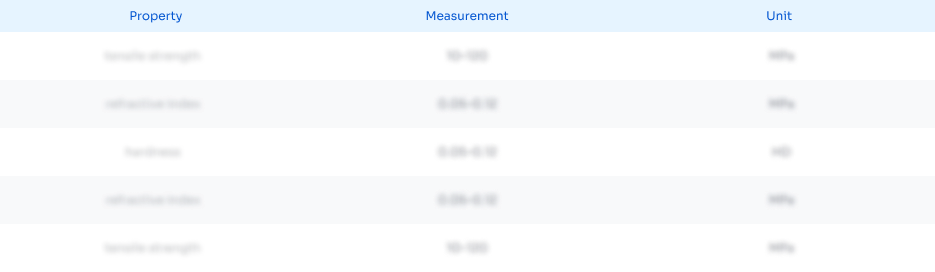
Abstract
Description
Claims
Application Information

- R&D Engineer
- R&D Manager
- IP Professional
- Industry Leading Data Capabilities
- Powerful AI technology
- Patent DNA Extraction
Browse by: Latest US Patents, China's latest patents, Technical Efficacy Thesaurus, Application Domain, Technology Topic, Popular Technical Reports.
© 2024 PatSnap. All rights reserved.Legal|Privacy policy|Modern Slavery Act Transparency Statement|Sitemap|About US| Contact US: help@patsnap.com