Special blade swinging type hydraulic cylinder for robot motion joint
A robot motion, swinging technology, applied in the directions of manipulators, mechanical equipment, engine components, etc., can solve the problems of large size, inability to withstand overturning moment, and not suitable for robot kinematic joints, etc., to achieve high torque density, simple structure, internal Small leak effect
- Summary
- Abstract
- Description
- Claims
- Application Information
AI Technical Summary
Problems solved by technology
Method used
Image
Examples
Embodiment Construction
[0017] Special vane swing hydraulic cylinder for robot kinematic joints, see figure 1 , figure 2 : It includes an upper end cover 1, a rotating shaft 2, a cylinder body 3, a stator 4, and a lower end cover 5. The outer ring surface of the axial middle region of the rotating shaft 2 is provided with a side convex ring 6, and the radial direction of the side convex ring 6 is provided with a side The convex blade 7, the side convex blade 7, the side convex ring 6 and the rotating shaft 2 form an integral structure. The upper end cover 1 is set on the rotating shaft 2 and is located on the upper part of the side convex ring 6. The lower end cover 5 is set on the rotating shaft 2 and is located on the side convex ring 6. The lower part of the side convex blade 7 is in the zero state, and the other radial end of the side convex blade 7 is arranged with a fixed piece 4, the inner wall of the fixed piece 4 and the outer wall of the side convex ring 6 are arranged with a gap, and the ...
PUM
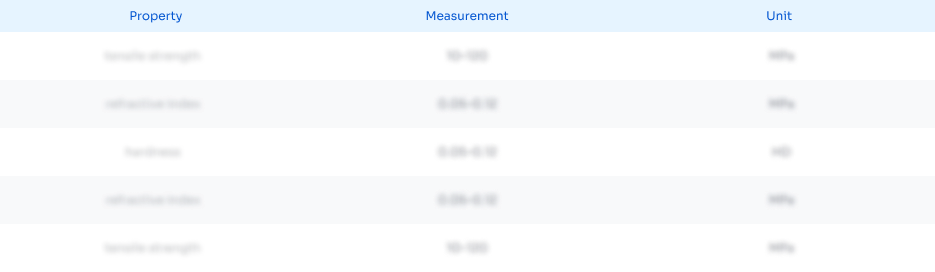
Abstract
Description
Claims
Application Information

- R&D
- Intellectual Property
- Life Sciences
- Materials
- Tech Scout
- Unparalleled Data Quality
- Higher Quality Content
- 60% Fewer Hallucinations
Browse by: Latest US Patents, China's latest patents, Technical Efficacy Thesaurus, Application Domain, Technology Topic, Popular Technical Reports.
© 2025 PatSnap. All rights reserved.Legal|Privacy policy|Modern Slavery Act Transparency Statement|Sitemap|About US| Contact US: help@patsnap.com