Direct drive type sinusoidal magnetic field composite permanent magnet motor
A permanent magnet motor, composite technology, applied in the direction of electrical components, electromechanical devices, magnetic circuit static parts, etc.
- Summary
- Abstract
- Description
- Claims
- Application Information
AI Technical Summary
Problems solved by technology
Method used
Image
Examples
Embodiment 1
[0021] Embodiment one: see figure 1 , the direct-drive sinusoidal magnetic field composite permanent magnet motor includes a self-controlled permanent magnet motor and a magnetic field modulation magnetic gear, which is characterized in that the permanent magnet motor and the magnetic gear both adopt a sinusoidal magnetized permanent magnet structure; and both Those are concentrically assembled into a double-stator double-rotor structure, that is, the outer rotor 4 and outer stator 7 that constitute the magnetic gear and the inner rotor 5 and inner stator 15 that constitute the permanent magnet motor adopt a sleeve-type structure to form a concentric structure.
Embodiment 2
[0022] Embodiment two: see figure 1 , figure 2 , image 3 , this embodiment is basically the same as Embodiment 1, and the special features are as follows: the outer rotor 4 is a cup-shaped rotor, and its cup-shaped bottom is fixedly connected with an outer rotor central shaft 1; the outer stator 7 is a cylindrical body, which is composed of Iron core blocks and non-magnetic materials are alternately spaced circumferentially, one end of which is directly connected to an end cover 2b of a frame 3 through an axial support 12, and the other end is connected to the inner stator 15 through a radial disc The inner end of the inner rotor is fixedly connected; the inner rotor 5 is a cylindrical body, which consists of an outer permanent magnet 8, an outer iron yoke 9, a stainless steel magnetic isolation cylinder, an inner iron yoke 10 and an inner layer The permanent magnet 11 is set, and the two ends of the stainless steel magnetic isolation cylinder are supported by two bearing...
Embodiment 3
[0030] Embodiment 3: This embodiment is basically the same as Embodiment 2. Its structure and working principle are as follows: the main shaft 1 of the sinusoidal magnetic field composite permanent magnet motor is connected with the outer rotor 4, and the output is low-speed and high-torque. The outer rotor permanent magnet 6, the inner rotor The outer permanent magnet 8 of the rotor 5 and the inner permanent magnet 11 are all sinusoidal magnetization (Halbach) structures, and the number of pole pairs of the inner rotor is P 2 , the number of outer rotor pole pairs P 1 , and P 1 >P 2. Therefore, the rotation speed of the outer rotor 4 is low, and the rotation speed of the inner rotor 5 is high. Between the outer rotor 4 and the inner rotor 5 is a reluctance type outer stator 7, and the reluctance type stator has N s A uniformly distributed iron core tooth pole, the slot is filled with non-magnetic material to enhance the mechanical strength. The outer permanent magnet 8 o...
PUM
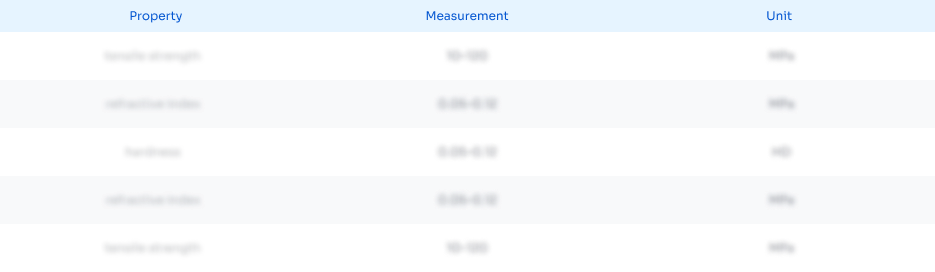
Abstract
Description
Claims
Application Information

- Generate Ideas
- Intellectual Property
- Life Sciences
- Materials
- Tech Scout
- Unparalleled Data Quality
- Higher Quality Content
- 60% Fewer Hallucinations
Browse by: Latest US Patents, China's latest patents, Technical Efficacy Thesaurus, Application Domain, Technology Topic, Popular Technical Reports.
© 2025 PatSnap. All rights reserved.Legal|Privacy policy|Modern Slavery Act Transparency Statement|Sitemap|About US| Contact US: help@patsnap.com