Preparation method for low temperature-resistant chlorinated polyethylene rubber
A technology of chlorinated polyethylene and low-temperature resistance, which is applied in the field of preparation of chlorinated polyethylene rubber, can solve the problems of poor low-temperature resistance of chlorinated polyethylene rubber, and achieve stability, increase production costs, and increase low-temperature resistance Effect
- Summary
- Abstract
- Description
- Claims
- Application Information
AI Technical Summary
Problems solved by technology
Method used
Examples
Embodiment 1
[0032] A preparation method of low-temperature-resistant chlorinated polyethylene rubber, the preparation method comprising the steps of:
[0033] S1, prepare the batching kettle and collect high-density polyethylene with a molecular weight of 200,000-300,000, high-density polyethylene with a molecular weight of 150,000-250,000 and sufficient chlorine for standby;
[0034] S2, add a certain amount of water to the batching kettle, start stirring, add emulsifier, dispersant and initiator, and then mix high-density polyethylene with a molecular weight of 200,000-300,000 and high-density polyethylene with a molecular weight of 150,000-250,000 according to the formulation Add it into the batching kettle, and use compressed air to press the chlorinated polyethylene material into the chlorination kettle after stirring evenly;
[0035] S3, add a certain amount of water to the phase chlorination kettle, pass hot water through the jacket until the temperature of the chlorinated polyethy...
Embodiment 2
[0041] A preparation method of low-temperature-resistant chlorinated polyethylene rubber, the preparation method comprising the steps of:
[0042] S1, prepare the batching kettle and collect high-density polyethylene with a molecular weight of 200,000-300,000, high-density polyethylene with a molecular weight of 150,000-250,000 and sufficient chlorine for standby;
[0043] S2, add a certain amount of water to the batching kettle, start stirring, add emulsifier, dispersant and initiator, and then mix high-density polyethylene with a molecular weight of 200,000-300,000 and high-density polyethylene with a molecular weight of 150,000-250,000 according to the formulation Add it into the batching kettle, and use compressed air to press the chlorinated polyethylene material into the chlorination kettle after stirring evenly;
[0044] S3, add a certain amount of water to the phase chlorination kettle, pass hot water through the jacket until the temperature of the chlorinated polyethy...
Embodiment 3
[0050] A preparation method of low-temperature-resistant chlorinated polyethylene rubber, the preparation method comprising the steps of:
[0051] S1, prepare the batching kettle and collect high-density polyethylene with a molecular weight of 200,000-300,000, high-density polyethylene with a molecular weight of 150,000-250,000 and sufficient chlorine for standby;
[0052] S2, add a certain amount of water to the batching kettle, start stirring, add emulsifier, dispersant and initiator, and then mix high-density polyethylene with a molecular weight of 200,000-300,000 and high-density polyethylene with a molecular weight of 150,000-250,000 according to the formulation Add it into the batching kettle, and use compressed air to press the chlorinated polyethylene material into the chlorination kettle after stirring evenly;
[0053] S3, add a certain amount of water to the phase chlorination kettle, pass hot water through the jacket until the temperature of the chlorinated polyethy...
PUM
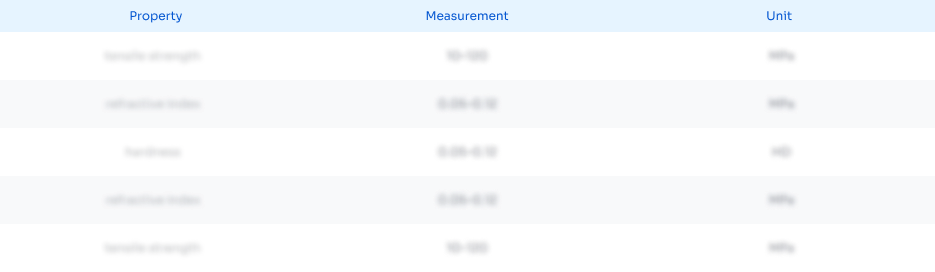
Abstract
Description
Claims
Application Information

- Generate Ideas
- Intellectual Property
- Life Sciences
- Materials
- Tech Scout
- Unparalleled Data Quality
- Higher Quality Content
- 60% Fewer Hallucinations
Browse by: Latest US Patents, China's latest patents, Technical Efficacy Thesaurus, Application Domain, Technology Topic, Popular Technical Reports.
© 2025 PatSnap. All rights reserved.Legal|Privacy policy|Modern Slavery Act Transparency Statement|Sitemap|About US| Contact US: help@patsnap.com