Dual-coil magneto-rheological valve with damping gap being automatically adjusted in liquid flow direction
A magneto-rheological valve, automatic adjustment technology, applied in the direction of fluid pressure actuation device, valve details, valve device, etc., can solve the problems of complex control system, large space occupation, poor controllability, etc., and achieve a large adjustable range, The effect of stable working performance and wide adjustment range of pressure drop
- Summary
- Abstract
- Description
- Claims
- Application Information
AI Technical Summary
Problems solved by technology
Method used
Image
Examples
Embodiment Construction
[0021] Below in conjunction with accompanying drawing and embodiment the present invention will be further described:
[0022] figure 1 Shown is the structure diagram of the present invention. Mainly include: left limit bolt 1, left end cover 2, left return spring 3, valve body 4, left spool piston 5, spool 6, left excitation coil 7, bobbin frame 8, right excitation coil 9, right spool Piston 10, right return spring 11, right end cover 12 and right limit bolt 13.
[0023] figure 2 Shown is the sectional view of the bobbin of the present invention. The winding frame 8 is processed with a sealing ring groove C, a sealing ring groove G, a lead wire groove E, a winding groove D and a winding groove F. The left excitation coil 7 is wound in the winding slot D of the bobbin 8 , the right exciting coil 9 is wound in the winding slot F of the bobbin 8 , and its lead wire is drawn from the valve body 4 through the lead slot E of the bobbin 8 . out of the lead hole.
[0024] im...
PUM
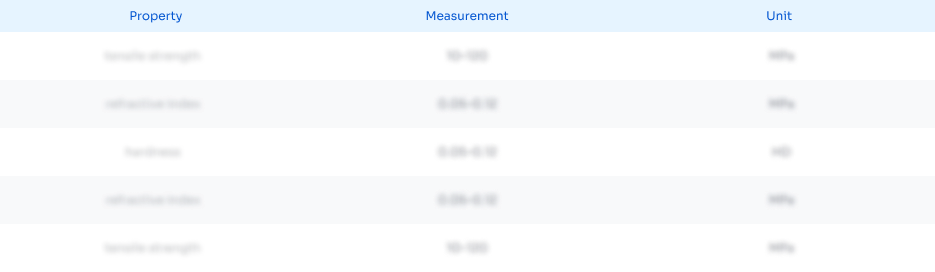
Abstract
Description
Claims
Application Information

- Generate Ideas
- Intellectual Property
- Life Sciences
- Materials
- Tech Scout
- Unparalleled Data Quality
- Higher Quality Content
- 60% Fewer Hallucinations
Browse by: Latest US Patents, China's latest patents, Technical Efficacy Thesaurus, Application Domain, Technology Topic, Popular Technical Reports.
© 2025 PatSnap. All rights reserved.Legal|Privacy policy|Modern Slavery Act Transparency Statement|Sitemap|About US| Contact US: help@patsnap.com