Roller singeing and sizing process for purified cotton warp
A cylinder and warp technology, applied in the continuous processing of textile materials, processing of textile materials, textiles and papermaking, etc., can solve the problem of serious fabric pilling and other problems
- Summary
- Abstract
- Description
- Claims
- Application Information
AI Technical Summary
Problems solved by technology
Method used
Image
Examples
Embodiment
[0017] like Figure 1-2 As shown, a pure cotton warp yarn cylinder singeing sizing process includes the following steps: warp yarn unwinding - first roller guide roller - cylinder singeing - second roller guide roller - sizing - drying - - guide rollers - rewinding; of which:
[0018] (1) Cylinder singeing: The cylinder singeing machine is singeed by the contact between the red-hot cylinder and the cotton cloth, and the contact area between the fabric and the cylinder is controlled by adjusting the roller roller, and the wrap angle is determined and controlled according to the specifications of the warp 150-175°, the rotation direction of the cylinder is opposite to the advancing direction of the cotton cloth, the rotation speed of the cylinder is 20-30m / min, and the advancing speed of the cotton cloth is 70-80m / min; the number of cylinders is 2-4. Etc., more than two cylinders can be singeed on both sides of the same warp beam, and the friction between the warp and the cylin...
PUM
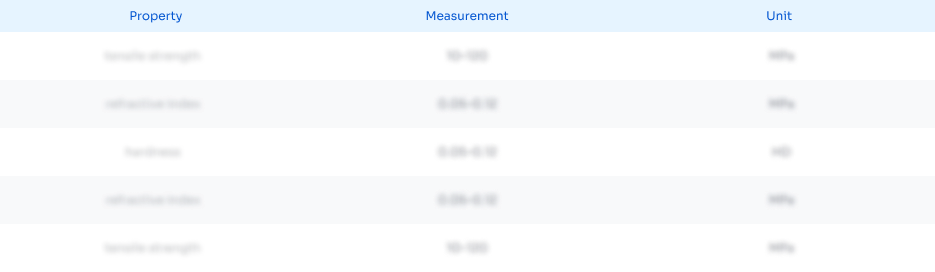
Abstract
Description
Claims
Application Information

- R&D
- Intellectual Property
- Life Sciences
- Materials
- Tech Scout
- Unparalleled Data Quality
- Higher Quality Content
- 60% Fewer Hallucinations
Browse by: Latest US Patents, China's latest patents, Technical Efficacy Thesaurus, Application Domain, Technology Topic, Popular Technical Reports.
© 2025 PatSnap. All rights reserved.Legal|Privacy policy|Modern Slavery Act Transparency Statement|Sitemap|About US| Contact US: help@patsnap.com