Composite core and manufacturing method thereof
A manufacturing method and composite core technology, applied in the field of hygiene products, can solve problems such as inability to improve core utilization and cross-layer conduction, poor instantaneous liquid capture ability, and drop, so as to improve temporary liquid storage capacity and improve absorption speed, improving the effect of multiple absorption
- Summary
- Abstract
- Description
- Claims
- Application Information
AI Technical Summary
Problems solved by technology
Method used
Image
Examples
Embodiment 1
[0044] Such as Figure 1~2 As shown, a composite core includes a surface layer 1, a bottom layer 3, and an absorbent layer 6 between the surface layer 1 and the bottom layer 3.
[0045] The absorbing layer 6 includes a layer of water-absorbing fiber layer 2 and SAP4 spread on the upper and lower surfaces of the water-absorbing fiber layer 2 and in the gap. The water-absorbing fiber layer 2 is a fluffy non-woven fabric. A plurality of guide holes 5 are opened between the surface layer 1 and the uppermost water-absorbing fiber layer 2 . The guide holes 5 penetrate the surface layer 1 .
[0046] A plurality of flow guide channels 7 are arranged between the bottom layer 3 and the lowermost water-absorbing fiber layer 2 . Each diversion channel 7 is continuous, and there are multiple diversion channels 7 on the same plane layer along the horizontal and vertical directions, distributed in a rectangular grid.
[0047] The junction of the water-absorbent fiber layer 2 and the dive...
Embodiment 2
[0070] Such as Figure 3-4 As shown, the embodiment 1 is repeated, the difference is that the arrangement of the guide holes 5 is different. The water-absorbing fiber layer 2 has two layers. A plurality of guide channels 7 on the same plane layer are distributed in a rhombus grid shape. The junction of the water-absorbing fiber layer 2 and the flow guide channel 7 is provided with an arched portion 8 facing the flow guide channel 7 . Processing method is similar to embodiment 1.
Embodiment 3
[0072] Such as Figure 5-6 Shown, repeat embodiment 1, the difference is: the depth of different diversion holes 5 is different. The guide holes 5 are symmetrically distributed in the middle area along the longitudinal centerline of the core.
[0073] The water-absorbing fiber layer 2 is provided with three layers. A plurality of guide channels 7 on the same plane layer are distributed in a hyperbola. The junction of the water-absorbing fiber layer 2 and the flow guide channel 7 is provided with an arched portion 8 facing the flow guide channel 7 .
[0074] Processing method is similar to embodiment 1.
PUM
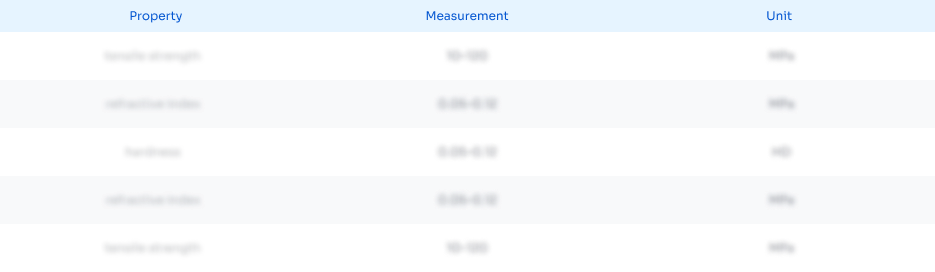
Abstract
Description
Claims
Application Information

- R&D
- Intellectual Property
- Life Sciences
- Materials
- Tech Scout
- Unparalleled Data Quality
- Higher Quality Content
- 60% Fewer Hallucinations
Browse by: Latest US Patents, China's latest patents, Technical Efficacy Thesaurus, Application Domain, Technology Topic, Popular Technical Reports.
© 2025 PatSnap. All rights reserved.Legal|Privacy policy|Modern Slavery Act Transparency Statement|Sitemap|About US| Contact US: help@patsnap.com