Method and device of full-domain cutting force modeling in rotary ultrasonic vibration milling
An ultrasonic vibration and rotary ultrasonic technology, applied in the field of ultrasonic vibration machining, can solve the problems of complex rotary ultrasonic vibration machining process, numerous process parameters, and the inability to predict the machining process by the empirical model of cutting force.
- Summary
- Abstract
- Description
- Claims
- Application Information
AI Technical Summary
Problems solved by technology
Method used
Image
Examples
Embodiment Construction
[0020] In order to make the purpose, technical solutions and advantages of the present invention clearer, the technical solutions in the present invention will be clearly and completely described below in conjunction with the accompanying drawings in the embodiments of the present invention. Obviously, the described embodiments are the embodiment of the present invention. Some, but not all, embodiments. Based on the embodiments of the present invention, all other embodiments obtained by persons of ordinary skill in the art without making creative efforts belong to the protection scope of the present invention.
[0021] As an aspect of the embodiment of the present invention, this embodiment provides a global cutting force modeling method for rotary ultrasonic vibration milling, refer to figure 1 , is a flow chart of a global cutting force modeling method for rotary ultrasonic vibration milling in an embodiment of the present invention, including:
[0022] S1. By analyzing the...
PUM
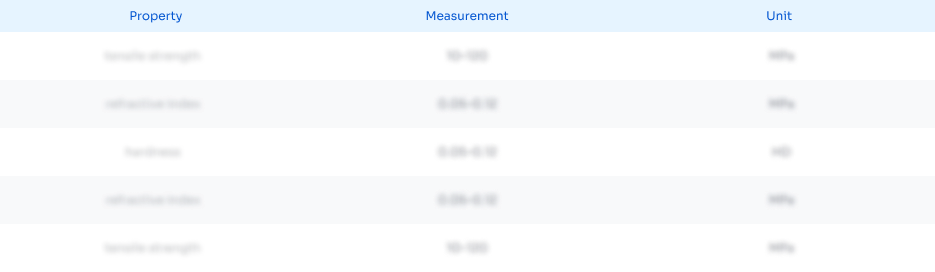
Abstract
Description
Claims
Application Information

- R&D
- Intellectual Property
- Life Sciences
- Materials
- Tech Scout
- Unparalleled Data Quality
- Higher Quality Content
- 60% Fewer Hallucinations
Browse by: Latest US Patents, China's latest patents, Technical Efficacy Thesaurus, Application Domain, Technology Topic, Popular Technical Reports.
© 2025 PatSnap. All rights reserved.Legal|Privacy policy|Modern Slavery Act Transparency Statement|Sitemap|About US| Contact US: help@patsnap.com