Variable stiffness flexible actuator
A flexible driver and variable stiffness technology, applied in the direction of manipulators, manufacturing tools, joints, etc., can solve the problems of small adjustment range, insufficient compactness of driving elements and transmission mechanisms, complex joint structure, etc., and achieve simple control and good flexible dynamic characteristics , good impact resistance effect
- Summary
- Abstract
- Description
- Claims
- Application Information
AI Technical Summary
Problems solved by technology
Method used
Image
Examples
Embodiment 1
[0032] Combine below Figure 1-Figure 5 Embodiment 1 will be described in detail.
[0033] figure 1 It is a schematic diagram of the three-dimensional structure of the variable stiffness flexible driver described in the present invention, figure 2 It is a schematic diagram of the internal structure of an embodiment of the variable stiffness flexible actuator of the present invention, image 3 for figure 2 The schematic diagram of the structure of the variable stiffness flexible drive motor shown in , such as Figure 1-Figure 3 As shown, the variable stiffness flexible driver of the present invention includes a power transmission mechanism, a stiffness adjustment mechanism and a stiffness output mechanism, wherein the power transmission mechanism includes a gear transmission mechanism and two motors 17, and the two motors 17 are arranged in parallel, and each motor 17 includes a motor base 17.3, a motor main body 17.2 and a motor output shaft 17.1, and the power is input ...
Embodiment 2
[0042] Combine below Figure 6-Figure 9 This embodiment will be described in detail.
[0043] Figure 6 It is a schematic diagram of the internal structure of another embodiment of the variable stiffness flexible actuator of the present invention,
[0044] Figure 7 for Figure 6 The structural diagram of the stiffness adjustment mechanism of the variable stiffness flexible actuator shown in , such as Figure 6-Figure 7 As shown, the variable stiffness flexible driver of the present invention includes a power transmission mechanism, a stiffness adjustment mechanism and a stiffness output mechanism, wherein the power transmission mechanism includes a gear transmission mechanism and two motors 17, and the two motors 17 are arranged in parallel, and each motor 17 includes a motor base 17.3, a motor main body 17.2 and a motor output shaft 17.1, and the power is input to the gear transmission mechanism through the motor 17; the stiffness adjustment mechanism includes two four-b...
PUM
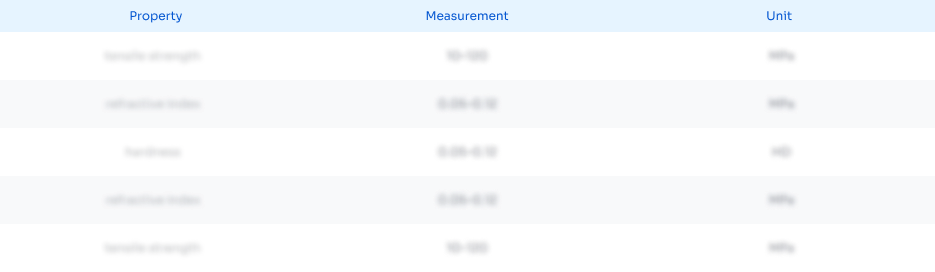
Abstract
Description
Claims
Application Information

- R&D
- Intellectual Property
- Life Sciences
- Materials
- Tech Scout
- Unparalleled Data Quality
- Higher Quality Content
- 60% Fewer Hallucinations
Browse by: Latest US Patents, China's latest patents, Technical Efficacy Thesaurus, Application Domain, Technology Topic, Popular Technical Reports.
© 2025 PatSnap. All rights reserved.Legal|Privacy policy|Modern Slavery Act Transparency Statement|Sitemap|About US| Contact US: help@patsnap.com