High-looseness tobacco sheet applied to low-temperature cigarette and production process
A tobacco sheet and low-temperature cigarette technology, which is applied in the fields of application, tobacco, and tobacco preparation, can solve the problems affecting the forming of tobacco sheet by rolling method, ineffective atomization and volatilization, poor thermal conductivity of tobacco substances, etc., and achieve solid content High, easy to mold, strong physiological satisfaction effect
- Summary
- Abstract
- Description
- Claims
- Application Information
AI Technical Summary
Problems solved by technology
Method used
Examples
Embodiment 1
[0025] A tobacco sheet with high porosity applied to low-temperature cigarettes, the specific preparation steps are as follows:
[0026] (1) Get the tobacco raw material and dry it and pulverize it into powder with a particle size of 30-100 meshes. The tobacco raw material includes any one or several mixtures of tobacco leaves, tobacco stems, and tobacco dust;
[0027] (2) Prepare the tobacco sheet raw material according to the following formula by mass percentage: 60% of tobacco raw material powder, 20% of glycerin, 5% of CMC, 0.4% of ammonium bicarbonate, 10% of fragrance type essence, and 4.6% of water in step (1);
[0028] (3) The raw materials in the step (2) are mixed evenly in proportion, and manufactured into tobacco flakes with a thickness of 0.10-0.15mm by rolling production process, and then sliced to form filaments of 0.8-0.9mm.
[0029] In the step (3), the process conditions for producing tobacco flakes by rolling method are as follows: the raw materials mixed ...
Embodiment 2
[0031] A tobacco sheet with high porosity applied to low-temperature cigarettes, the specific preparation steps are as follows:
[0032] (1) Get the tobacco raw material and dry it and pulverize it into powder with a particle size of 30-100 meshes. The tobacco raw material includes any one or several mixtures of tobacco leaves, tobacco stems, and tobacco dust;
[0033] (2) According to the formula of the following mass percentages, the raw material of tobacco slices is prepared: 57% of tobacco raw material powder, 24% of glycerin, 5% of sodium alginate, 0.6% of sodium bicarbonate, 8% of sweet flavor essence in step (1), Water 5.4%;
[0034] (3) The raw materials in the step (2) are mixed evenly in proportion, and manufactured into tobacco flakes with a thickness of 0.16-0.18 mm by a rolling production process, and then sliced into sheets of 50×30 mm.
[0035] In the step (3), the process conditions for producing tobacco flakes by rolling method are as follows: the raw mater...
Embodiment 3
[0037] A tobacco sheet with high porosity applied to low-temperature cigarettes, the specific preparation steps are as follows:
[0038] (1) Get the tobacco raw material and dry it and pulverize it into powder with a particle size of 30-100 meshes. The tobacco raw material includes any one or several mixtures of tobacco leaves, tobacco stems, and tobacco dust;
[0039] (2) According to the formula of the following mass percentages, the raw material of the tobacco sheet is prepared: 55% of tobacco raw material powder, 12% of propylene glycol, 14% of glycerin, 5% of guar gum, 0.8% of potassium aluminum sulfate, and tobacco base incense in the step (1). 10% essence, 3.2% water;
[0040](3) The raw materials in the step (2) are mixed evenly in proportion, and manufactured into tobacco flakes with a thickness of 0.12-0.13 mm by rolling method production process, and then sliced to form filaments of 0.8-0.9 mm.
[0041] In the step (3), the process conditions for producing tobacc...
PUM
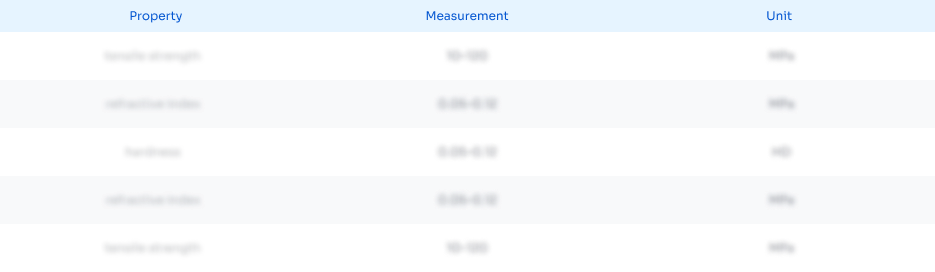
Abstract
Description
Claims
Application Information

- R&D
- Intellectual Property
- Life Sciences
- Materials
- Tech Scout
- Unparalleled Data Quality
- Higher Quality Content
- 60% Fewer Hallucinations
Browse by: Latest US Patents, China's latest patents, Technical Efficacy Thesaurus, Application Domain, Technology Topic, Popular Technical Reports.
© 2025 PatSnap. All rights reserved.Legal|Privacy policy|Modern Slavery Act Transparency Statement|Sitemap|About US| Contact US: help@patsnap.com