Integral valve casting and technology thereof
An integral, valve body technology, applied in the direction of casting molds, casting mold components, manufacturing tools, etc., can solve the problems of easy sintering, poor exhaust, easy formation of pores, etc., and achieves good bending resistance, compact structure, and is not easy to leaked effect
- Summary
- Abstract
- Description
- Claims
- Application Information
AI Technical Summary
Problems solved by technology
Method used
Image
Examples
Embodiment
[0069] The invention provides a processing technology for integral valve body castings, including mold inspection and cleaning, making sand shells and sand cores, sand core coating and drying, sand core drilling, sand cores and sand shells with shell assembly, modeling And pouring, the key technical steps are as follows:
[0070] 1) Using the coated sand shell type process, the main valve hole is placed with a Φ4.5mm core bone during core making, and the main sand core is assembled from multiple sand cores, and there is no gap at the assembly interface;
[0071] 2) Use a new type of high-temperature-resistant coating as the sand core coating, drill vent holes after drying the core, and check the main channel hole;
[0072] 3) When matching the shell, a special "E" sub-core support is used to fix the suspended sand core;
[0073] 4) When modeling, adopt resin sand buried shell technology, and control the size within ±0.4mm range,
[0074] 5) When pouring, use a special cold i...
PUM
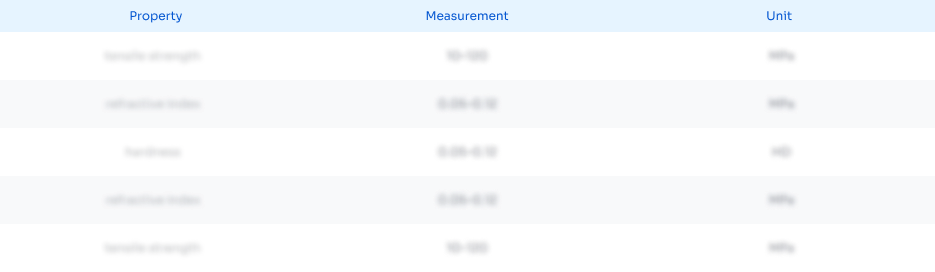
Abstract
Description
Claims
Application Information

- Generate Ideas
- Intellectual Property
- Life Sciences
- Materials
- Tech Scout
- Unparalleled Data Quality
- Higher Quality Content
- 60% Fewer Hallucinations
Browse by: Latest US Patents, China's latest patents, Technical Efficacy Thesaurus, Application Domain, Technology Topic, Popular Technical Reports.
© 2025 PatSnap. All rights reserved.Legal|Privacy policy|Modern Slavery Act Transparency Statement|Sitemap|About US| Contact US: help@patsnap.com