A method for oxygen-increased combustion of pulverized coal mixed with biomass
A biomass and admixture technology, which is applied in combustion methods, combustion using lump fuel and powder fuel, combustion equipment, etc. The problem of large difference in characteristics, etc., can reduce the loss of exhaust gas, increase the oxygen content, and reduce the generation amount.
- Summary
- Abstract
- Description
- Claims
- Application Information
AI Technical Summary
Problems solved by technology
Method used
Image
Examples
Embodiment 1
[0023] Biomass and coal powder are pre-mixed to form a blend before entering the furnace, and the calorific value ratio of biomass and coal powder is 1:5. The admixture is used as fuel and injected into the furnace by the oxygen-increased primary air. The oxygen content of the oxygen-increased primary air is 22%, the oxygen content of the oxygen-increased secondary air is 22%, and the excess air coefficient in the furnace is 1.1. The oxygen entering the furnace The volume flow accounts for 22% of the total gas volume flow entering the furnace.
Embodiment 2
[0025] Biomass and coal powder are pre-mixed to form a blend before entering the furnace, and the calorific value ratio of biomass and coal powder is 1:4. The mixture is used as fuel and injected into the furnace by the oxygen-increased primary air. The oxygen content of the oxygen-increased primary air is 27%, the oxygen content of the oxygen-increased secondary air is 23%, and the excess air coefficient in the furnace is 1.05. The oxygen entering the furnace The volume flow accounts for 24% of the total gas volume flow into the furnace.
Embodiment 3
[0027] The biomass and pulverized coal are pre-mixed to form a blend before entering the furnace, and the calorific value ratio of biomass and pulverized coal is 3:10. The admixture is used as fuel and injected into the furnace by the oxygen-increased primary air. The oxygen content of the oxygen-increased primary air is 30%, the oxygen content of the secondary air is 26%, the excess air coefficient in the furnace is 1, and the oxygen volume flow rate entering the furnace It accounts for 26% of the total gas volume flow into the furnace.
PUM
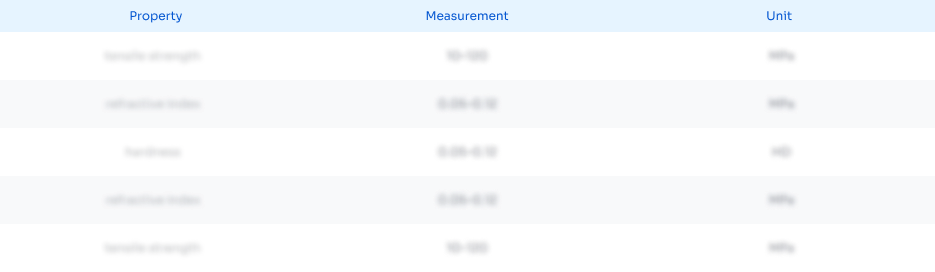
Abstract
Description
Claims
Application Information

- R&D Engineer
- R&D Manager
- IP Professional
- Industry Leading Data Capabilities
- Powerful AI technology
- Patent DNA Extraction
Browse by: Latest US Patents, China's latest patents, Technical Efficacy Thesaurus, Application Domain, Technology Topic, Popular Technical Reports.
© 2024 PatSnap. All rights reserved.Legal|Privacy policy|Modern Slavery Act Transparency Statement|Sitemap|About US| Contact US: help@patsnap.com