Hot melting reflective type road reticule coating
A road marking and reflective technology, used in reflective/signal coatings, anti-corrosion coatings, polyester coatings, etc., can solve problems such as cumbersome construction, and achieve the effects of short drying time, good reflectivity, and enhanced bonding strength
- Summary
- Abstract
- Description
- Claims
- Application Information
AI Technical Summary
Problems solved by technology
Method used
Image
Examples
Embodiment 1
[0031] Preparation of modified rosin-alkyd resin: Add 10Kg of rosin to 1.5Kg of maleic anhydride under nitrogen atmosphere and temperature of 150°C, heat up to 200°C for 1.5 hours, add 1.9Kg of glycerin, and then heat up to 275°C ℃ heat preservation reaction for 7 hours, remove small molecular compounds, and obtain modified rosin resin; 22.5Kg of methyl diphenyl glycolate and 7Kg of glycerin are transesterified to obtain monoglyceride, monoglyceride and phthalic anhydride 43Kg in The temperature is 222°C and the polyesterification reaction occurs for 0.75 hours in the presence of lithium hydroxide to obtain alkyd resin oligomers; the modified rosin resin and alkyd resin oligomers with a weight ratio of 4:1.1-1.3 are obtained at temperature React at 200°C for 1.5 hours to obtain modified rosin-alkyd resin.
[0032] Preparation of hot-melt reflective road marking paint: modified rosin-alkyd resin 20Kg, EVA resin 10Kg, filler 110Kg (heavy calcium carbonate 55Kg, quartz sand 25Kg,...
Embodiment 2
[0034]Preparation of modified rosin-alkyd resin: 10Kg of rosin was added to 1.6Kg of maleic anhydride under the conditions of nitrogen atmosphere and temperature of 155°C, the temperature was raised to 203°C for 1.25 hours, and 2.0Kg of glycerin was added, and then the temperature was raised to 270°C ℃ heat preservation reaction for 8 hours, remove small molecular compounds, and obtain modified rosin resin; 23Kg of methyl diphenyl glycolate and 6Kg of glycerin are transesterified to obtain monoglyceride, monoglyceride and phthalic anhydride 42Kg at temperature Under the conditions of 220°C and the presence of lithium hydroxide, a polyesterification reaction takes place for 1 hour to obtain an alkyd resin oligomer; a modified rosin resin and an alkyd resin oligomer with a weight ratio of 4:1.1-1.3 can be obtained at a temperature of React at 205°C for 1.25 hours to obtain a modified rosin-alkyd resin.
[0035] Preparation of hot-melt reflective road marking paint: modified rosi...
Embodiment 3
[0037] Preparation of modified rosin-alkyd resin: Add 10Kg of rosin to 1.7Kg of maleic anhydride under nitrogen atmosphere and temperature of 153°C, heat up to 205°C for 1 hour, add 1.8Kg of glycerin, and then heat up to 272°C ℃ heat preservation reaction for 7.5 hours to remove small molecular compounds to obtain modified rosin resin; 22Kg of methyl diphenyl glycolate and 6.5Kg of glycerin were transesterified to obtain monoglyceride, monoglyceride and phthalic anhydride 44Kg in The temperature is 225°C and the polyesterification reaction occurs for 0.5 hours in the presence of lithium hydroxide to obtain an alkyd resin oligomer; the modified rosin resin and alkyd resin oligomer with a weight ratio of 4:1.1-1.3 React at 210°C for 1 hour to obtain modified rosin-alkyd resin.
[0038] Preparation of hot-melt reflective road marking paint: modified rosin-alkyd resin 25Kg, EVA resin 5Kg, filler 120Kg (heavy calcium carbonate 65Kg, quartz sand 30Kg, talcum powder 25Kg), titanium d...
PUM
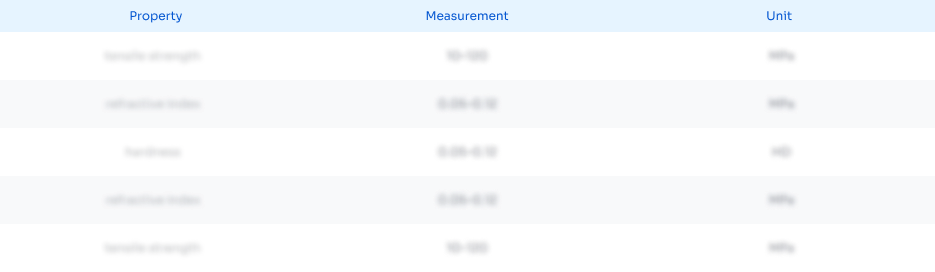
Abstract
Description
Claims
Application Information

- R&D
- Intellectual Property
- Life Sciences
- Materials
- Tech Scout
- Unparalleled Data Quality
- Higher Quality Content
- 60% Fewer Hallucinations
Browse by: Latest US Patents, China's latest patents, Technical Efficacy Thesaurus, Application Domain, Technology Topic, Popular Technical Reports.
© 2025 PatSnap. All rights reserved.Legal|Privacy policy|Modern Slavery Act Transparency Statement|Sitemap|About US| Contact US: help@patsnap.com