Seat back panel composite tooling
A tooling and decorative board technology, which is applied in the jointing of wooden veneers, manufacturing tools, wood processing appliances, etc., can solve the problems of easy wrinkling of fabrics and low product qualification rate, and achieve the effect of improving product qualification rate
- Summary
- Abstract
- Description
- Claims
- Application Information
AI Technical Summary
Problems solved by technology
Method used
Image
Examples
Embodiment Construction
[0028] like Figure 1-10As shown, a seat back trim compound tooling is used for compounding fabrics and seat back panels. It includes a composite mold and a fabric clamping mechanism 04. The composite mold includes an upper mold and a lower mold 01 parallel to each other. Two fabric clamping mechanisms 04 are arranged symmetrically between the upper mold and the lower mold 01, and the fabric clamping mechanisms 04 are respectively located on both sides of the composite mould. The upper mold includes an upper die 02 and two The side die 03 on the side; cooling water pipes are evenly arranged in the upper die 02 and the lower die 01 to accelerate cooling and recombination; it also includes a stand, which includes a vertical frame 05, a platform 06 and a top Frames 05 are vertically arranged symmetrically, between the vertical frames 05 are respectively provided with a platen 06 and a top plate 07, the platen 06 is located in the middle of the vertical frame 05, the top plate 07 ...
PUM
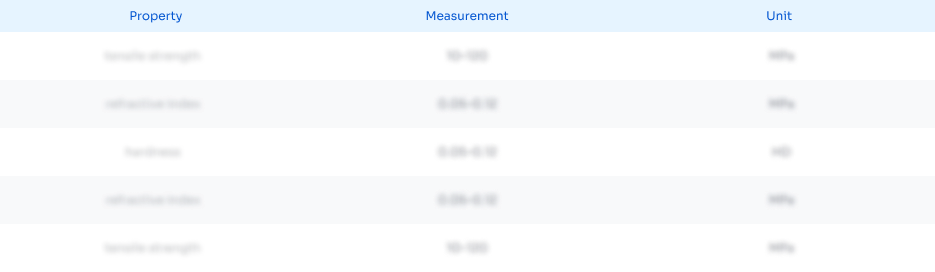
Abstract
Description
Claims
Application Information

- R&D Engineer
- R&D Manager
- IP Professional
- Industry Leading Data Capabilities
- Powerful AI technology
- Patent DNA Extraction
Browse by: Latest US Patents, China's latest patents, Technical Efficacy Thesaurus, Application Domain, Technology Topic, Popular Technical Reports.
© 2024 PatSnap. All rights reserved.Legal|Privacy policy|Modern Slavery Act Transparency Statement|Sitemap|About US| Contact US: help@patsnap.com