Novel mechanical arm joint
A technology of manipulators and joints, applied in the field of manipulators, can solve the problems of weak ability to change according to requirements, small driving torque, and influence of swing angle of manipulator joint shafts, etc., to achieve large output torque, ensure output torque, and guarantee The effect of swing angle
- Summary
- Abstract
- Description
- Claims
- Application Information
AI Technical Summary
Problems solved by technology
Method used
Image
Examples
Embodiment Construction
[0023] Below in conjunction with accompanying drawing and specific embodiment, the present invention will be further described:
[0024] Such as figure 1 , 4 , 5, a new type of mechanical arm joints, including swing cylinder drive and servo motor drive.
[0025] The swing cylinder driving device includes a cylinder body 7 , a swing cylinder rotor 5 , a cover plate 2 , and a cover plate connecting plate 1 . Two of the cover plates 2 are respectively installed on both sides of the cylinder body 7 through several cover plate screws 6 to seal the inside of the cylinder body 7 . A through hole is opened on the cover plate 2, the swing cylinder rotor 5 is installed in the cylinder body 7, and both sides protrude from the through hole. The cylinder body 7 is mounted on the cover connecting plate 1 through two cover plates 2 .
[0026] The two sides of the swing cylinder rotor 5 are equipped with a force arm rod 3 , and the end of the force arm rod 3 away from the swing cylinder r...
PUM
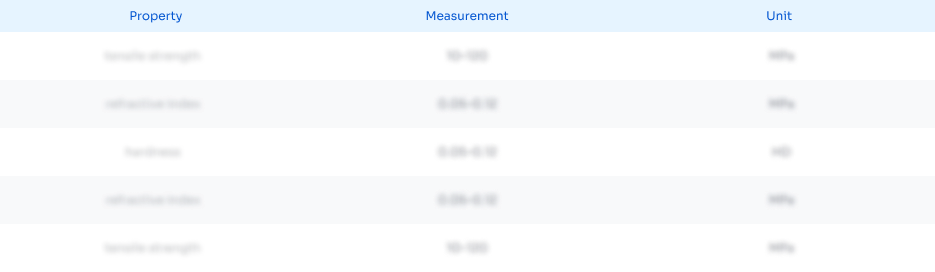
Abstract
Description
Claims
Application Information

- R&D
- Intellectual Property
- Life Sciences
- Materials
- Tech Scout
- Unparalleled Data Quality
- Higher Quality Content
- 60% Fewer Hallucinations
Browse by: Latest US Patents, China's latest patents, Technical Efficacy Thesaurus, Application Domain, Technology Topic, Popular Technical Reports.
© 2025 PatSnap. All rights reserved.Legal|Privacy policy|Modern Slavery Act Transparency Statement|Sitemap|About US| Contact US: help@patsnap.com