Model prediction torque control method based on duty ratio
A technology of torque control and model prediction, applied in control systems, control generators, vector control systems, etc., can solve problems such as high computational burden, high torque ripple, lack of theoretical design process, etc.
- Summary
- Abstract
- Description
- Claims
- Application Information
AI Technical Summary
Problems solved by technology
Method used
Image
Examples
Embodiment Construction
[0026] A duty cycle-based model predictive torque control method of the present invention will be described in detail below in conjunction with the embodiments and the accompanying drawings.
[0027]A kind of model predictive torque control method based on duty cycle of the present invention, comprises the steps:
[0028] 1) At time k, the electrical angular velocity ω of the motor rotor is controlled by the control system e , rotor position angle θ, motor ABC three-phase current i A (k), i B (k) and i C (k), DC bus voltage u dc (k) Sampling and solving the d, q axis component i of the ABC three-phase current d (k) and i q (k);
[0029] 2) The speed error Δω e The electromagnetic torque reference value T is calculated by the PI regulator e * , the stator flux reference value is a constant value ψ s * ;
[0030] 3) According to the d and q axis components i of the obtained ABC three-phase current d (k) and i q (k), use the torque formula to obtain the electromagne...
PUM
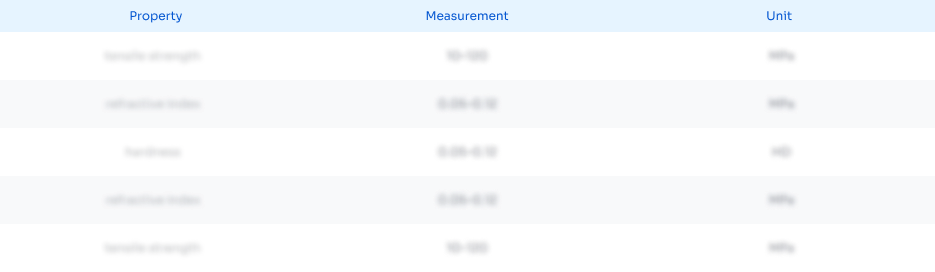
Abstract
Description
Claims
Application Information

- R&D
- Intellectual Property
- Life Sciences
- Materials
- Tech Scout
- Unparalleled Data Quality
- Higher Quality Content
- 60% Fewer Hallucinations
Browse by: Latest US Patents, China's latest patents, Technical Efficacy Thesaurus, Application Domain, Technology Topic, Popular Technical Reports.
© 2025 PatSnap. All rights reserved.Legal|Privacy policy|Modern Slavery Act Transparency Statement|Sitemap|About US| Contact US: help@patsnap.com