High-strength ceiling material and preparation method thereof
A ceiling and high-strength technology, which is applied in the field of high-strength ceiling materials and its preparation, can solve the problems of easy powdery fracture resistance and other problems, and achieve the goals of improving friability, improving comprehensive performance, improving strength and corrosion resistance Effect
- Summary
- Abstract
- Description
- Claims
- Application Information
AI Technical Summary
Problems solved by technology
Method used
Examples
Embodiment 1
[0025] A high-strength ceiling material, comprising the following raw materials in parts by weight:
[0026] 35 parts of modified phenolic resin, 8 parts of polytetrafluoroethylene, 8 parts of silica fume powder, 6 parts of hollow glass microspheres, 6 parts of sepiolite fiber, 3 parts of tourmaline powder, 3 parts of zinc borate, 2 parts of nano zinc oxide, 4 parts of expanded graphite, 6 parts of diatomaceous earth, 20 parts of coconut shell powder, 5 parts of bamboo charcoal powder, 4 parts of barley green pigment, 3 parts of nano-titanium dioxide, 4 parts of carbon nanotubes, 1.5 parts of silane coupling agent, 1.2 parts of antioxidant and 1.8 parts of flame retardant;
[0027] The preparation of modified phenolic resin comprises the following steps:
[0028] Stir and mix the phenolic resin and N-(4-hydroxyphenyl)maleimide corresponding to 5% of its weight evenly, heat up to 90 degrees Celsius, and react with stirring at a speed of 600 rpm for 20 minutes, slowly equivalen...
Embodiment 2
[0041] A high-strength ceiling material, comprising the following raw materials in parts by weight:
[0042] 45 parts of modified phenolic resin, 15 parts of polytetrafluoroethylene, 15 parts of silica fume powder, 12 parts of hollow glass microspheres, 12 parts of sepiolite fiber, 6 parts of tourmaline powder, 6 parts of zinc borate, 4 parts of nano zinc oxide, 8 parts of expanded graphite, 12 parts of diatomaceous earth, 30 parts of coconut shell powder, 10 parts of bamboo charcoal powder, 8 parts of barley green pigment, 7 parts of nano-titanium dioxide, 8 parts of carbon nanotubes, 3.2 parts of silane coupling agent, 2.5 parts of antioxidant and 3.6 parts of flame retardant;
[0043] The preparation of described modified phenolic resin comprises the following steps:
[0044] Stir and mix the phenolic resin and N-(4-hydroxyphenyl)maleimide corresponding to 5% of its weight evenly, heat up to 110 degrees Celsius, and react with stirring at a speed of 1000 rpm for 30 minutes...
Embodiment 3
[0057] A high-strength ceiling material, comprising the following raw materials in parts by weight:
[0058] 40 parts of modified phenolic resin, 12 parts of polytetrafluoroethylene, 12 parts of silica fume powder, 10 parts of hollow glass microspheres, 10 parts of sepiolite fiber, 4.5 parts of tourmaline powder, 4.5 parts of zinc borate, 3 parts of nano zinc oxide, 6 parts of expanded graphite, 10 parts of diatomaceous earth, 25 parts of coconut shell powder, 8 parts of bamboo charcoal powder, 6 parts of barley green pigment, 5 parts of nano-titanium dioxide, 6 parts of carbon nanotubes, 2.6 parts of silane coupling agent, 1.8 parts of antioxidant And 2.8 parts of flame retardant.
[0059] The preparation of modified phenolic resin comprises the following steps:
[0060] Stir and mix the phenolic resin and N-(4-hydroxyphenyl)maleimide corresponding to 5% of its weight evenly, heat up to 100 degrees Celsius, and react with stirring at a speed of 800 rpm for 25 minutes. 30% h...
PUM
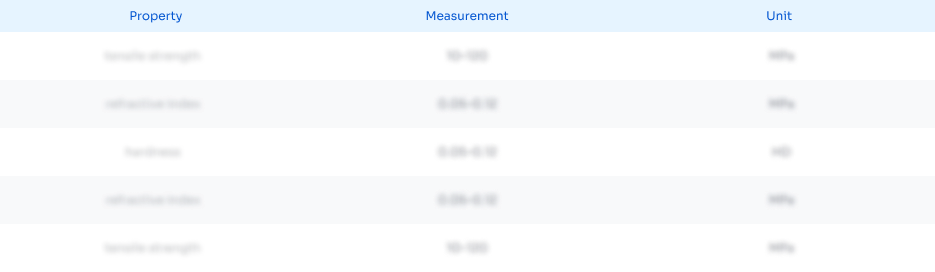
Abstract
Description
Claims
Application Information

- R&D Engineer
- R&D Manager
- IP Professional
- Industry Leading Data Capabilities
- Powerful AI technology
- Patent DNA Extraction
Browse by: Latest US Patents, China's latest patents, Technical Efficacy Thesaurus, Application Domain, Technology Topic, Popular Technical Reports.
© 2024 PatSnap. All rights reserved.Legal|Privacy policy|Modern Slavery Act Transparency Statement|Sitemap|About US| Contact US: help@patsnap.com