Producing method of glass fiber cloth
A glass fiber cloth and a production method technology, applied in the field of materials, can solve the problems of insufficient strength, increased cost, easy burrs, etc., and achieve the effects of light and thin texture, material saving, and thin texture
- Summary
- Abstract
- Description
- Claims
- Application Information
AI Technical Summary
Problems solved by technology
Method used
Examples
Embodiment 1
[0009] A method for making glass fiber cloth, comprising the following main steps: the raw materials used are: 1-3 parts of aluminum oxide, 5-8 parts of zinc oxide, 12 parts of sodium benzoate, 12 parts of methyl butyrate, 6 parts of sodium methyl phosphate 12 parts of castor oil, 11 parts of ethylene oxide, 18 parts of diethanolamine, 17 parts of sodium lauryl sulfate, 19 parts of sunflower oil, 11 parts of sodium aluminate, 8 parts of alanine, dipropylene glycol butyl ether 8 parts of dipropylene glycol monoalkyl, 12 parts of aluminum nitrate, 4 parts of rutile titanium dioxide, 3 parts of sunset yellow, 6 parts of vitamin C ethyl ether, 1 part of cocamidopropyl betaine, 10 parts of lactic acid and corn starch 8 servings.
[0010] The above raw materials are mixed and heated to 120 degrees Celsius, reacted under normal pressure for 12 minutes, then injected into the injection molding machine, and extruded according to the specified thickness to obtain glass fiber cloth.
Embodiment 2
[0012] A method for making glass fiber cloth, comprising the following major steps: the raw materials used are: 3 parts of aluminum oxide, 8 parts of zinc oxide, 12 parts of sodium benzoate, 12 parts of methyl butyrate, 6 parts of sodium methyl phosphate, castor oil 12 parts, 11 parts of ethylene oxide, 18 parts of diethanolamine, 17 parts of sodium lauryl sulfate, 19 parts of sunflower oil, 11 parts of sodium aluminate, 8 parts of alanine, dipropylene glycol butyl ether and other dipropylene glycol mono 8 parts of alkyl, 12 parts of aluminum nitrate, 7 parts of rutile titanium dioxide, 8 parts of sunset yellow, 11 parts of vitamin C ethyl ether, 10 parts of cocamidopropyl betaine, 19 parts of lactic acid and 10 parts of corn starch.
[0013] After the above-mentioned raw materials are mixed, they are heated to 146 degrees Celsius, reacted under normal pressure conditions for 19 minutes, then injected into an injection molding machine, and extruded according to the specified th...
Embodiment 3
[0015] A method for making glass fiber cloth, comprising the following main steps: raw materials used are: 2 parts of aluminum oxide, 6 parts of zinc oxide, 9 parts of sodium benzoate, 5 parts of methyl butyrate, 5 parts of sodium methyl phosphate, castor oil 11 parts, 8 parts of ethylene oxide, 17 parts of diethanolamine, 12 parts of sodium lauryl sulfate, 12 parts of sunflower oil, 10 parts of sodium aluminate, 3 parts of alanine, dipropylene glycol butyl ether and other dipropylene glycol mono 4 parts of alkyl, 11 parts of aluminum nitrate, 5 parts of rutile titanium dioxide, 5 parts of sunset yellow, 7 parts of vitamin C ethyl ether, 2 parts of cocamidopropyl betaine, 12 parts of lactic acid and 9 parts of corn starch.
[0016] After the above-mentioned raw materials are mixed, they are heated to 141 degrees Celsius, reacted under normal pressure conditions for 13 minutes, then injected into an injection molding machine, and extruded according to the specified thickness to ...
PUM
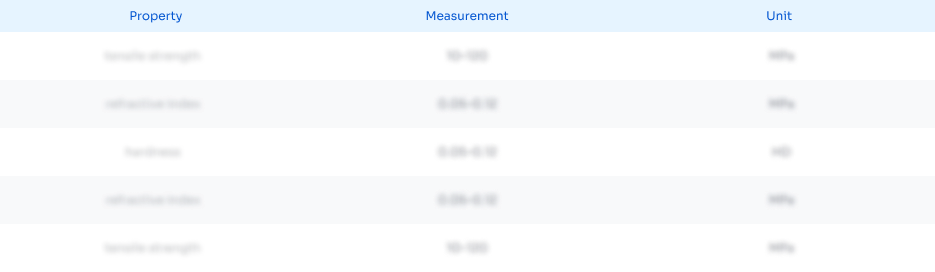
Abstract
Description
Claims
Application Information

- R&D
- Intellectual Property
- Life Sciences
- Materials
- Tech Scout
- Unparalleled Data Quality
- Higher Quality Content
- 60% Fewer Hallucinations
Browse by: Latest US Patents, China's latest patents, Technical Efficacy Thesaurus, Application Domain, Technology Topic, Popular Technical Reports.
© 2025 PatSnap. All rights reserved.Legal|Privacy policy|Modern Slavery Act Transparency Statement|Sitemap|About US| Contact US: help@patsnap.com