Manufacturing method of composite electromagnetic valve
A technology for electromagnetic valves and manufacturing methods, which is applied in the direction of metal material coating process, coating, molten spraying, etc., and can solve the problems of reduced sealing performance of valve body, failure of corrosion resistance performance to meet requirements, easy corrosion of electromagnetic working parts, etc. , to improve the sealing performance, solve the problem of acid and alkali corrosion resistance, and not easy to age
- Summary
- Abstract
- Description
- Claims
- Application Information
AI Technical Summary
Problems solved by technology
Method used
Examples
Embodiment 1
[0022] A manufacturing method of a composite electromagnetic valve, the manufacturing method of the composite electromagnetic valve comprises the following steps:
[0023] S1, 12 parts of polytetrafluoroethylene are placed in the mould, Mg 2 SiO 4 3 parts, 0.6 parts of nano-alumina, 0.01 part of zirconium nitride, and 0.01 part of titanium dioxide are filled into polytetrafluoroethylene to obtain fillers for later use;
[0024] S2. Put a single valve body made of metal into the mold, put the filling material in step S1 into the mold, close the mold, put the mold into a high-temperature furnace to heat up to 520°C and keep it warm for 48 minutes, then pressurize Mold, after blowing cold nitrogen on the mold for 40 minutes during the pressurization process, open the mold to obtain the valve semi-finished product;
[0025] S3. Spray 5 parts of chromium carbide onto the surface of the valve body using supersonic flame spraying technology to obtain the final product
[0026] Whe...
Embodiment 2
[0028] A manufacturing method of a composite electromagnetic valve, the manufacturing method of the composite electromagnetic valve comprises the following steps:
[0029] S1, 10 parts of polytetrafluoroethylene is placed in the mould, Mg 2 SiO 4 2 parts, 0.5 parts of nano-alumina, 0.02 parts of zirconium nitride, and 0.02 parts of titanium dioxide are filled into polytetrafluoroethylene to obtain fillers for later use;
[0030] S2. Put a single valve body made of metal into the mold, put the filling material in step S1 into the mold, close the mold, put the mold into a high-temperature furnace to heat up to 550°C, keep it warm for 55 minutes, and then pressurize Mold, after blowing cold nitrogen on the mold for 45 minutes during the pressurization process, open the mold to obtain the valve semi-finished product;
[0031] S3. Spray 4 parts of chromium carbide on the surface of the valve body by supersonic flame spraying technology to obtain the final product.
[0032] Where...
Embodiment 3
[0034] A manufacturing method of a composite electromagnetic valve, the manufacturing method of the composite electromagnetic valve comprises the following steps:
[0035] S1, 15 parts of polytetrafluoroethylene is placed in the mould, Mg 2 SiO 4 4 parts, 0.7 parts of nano-alumina, 0.01 part of zirconium nitride, and 0.01 part of titanium dioxide are filled into polytetrafluoroethylene to obtain fillers for later use;
[0036] S2. Put a single valve body made of metal into the mold, put the filling material in step S1 into the mold, close the mold, put the mold into a high-temperature furnace and heat it up to 500°C, keep it warm for 55 minutes, and then pressurize Mold, after blowing cold nitrogen on the mold for 45 minutes during the pressurization process, open the mold to obtain the valve semi-finished product;
[0037] S3. Spraying 5 parts of chromium carbide on the surface of the valve body by supersonic flame spraying technology to obtain the final product.
PUM
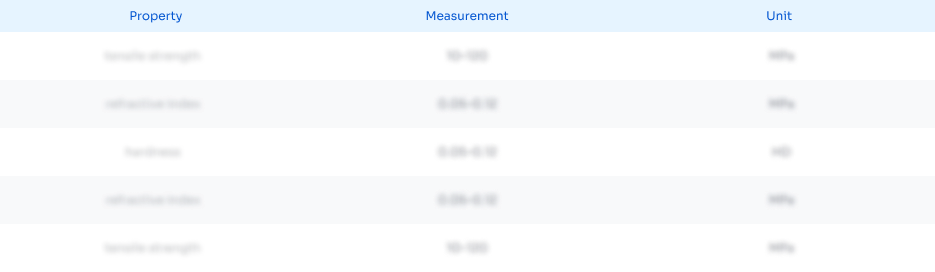
Abstract
Description
Claims
Application Information

- Generate Ideas
- Intellectual Property
- Life Sciences
- Materials
- Tech Scout
- Unparalleled Data Quality
- Higher Quality Content
- 60% Fewer Hallucinations
Browse by: Latest US Patents, China's latest patents, Technical Efficacy Thesaurus, Application Domain, Technology Topic, Popular Technical Reports.
© 2025 PatSnap. All rights reserved.Legal|Privacy policy|Modern Slavery Act Transparency Statement|Sitemap|About US| Contact US: help@patsnap.com