Camera module aligning method
A camera module and lens technology, which is used in metal processing, workpiece clamping devices, metal processing equipment, etc., can solve problems such as deviation of results, no suggestion, manual adjustment errors, etc., to eliminate inconsistencies, adjust speed quickly, and improve The effect of assembly efficiency
- Summary
- Abstract
- Description
- Claims
- Application Information
AI Technical Summary
Problems solved by technology
Method used
Image
Examples
Embodiment Construction
[0021] The present invention will be further described below in conjunction with the accompanying drawings and embodiments.
[0022] refer to Figures 1 to 3 , in a preferred embodiment: the specific steps of the alignment method of the camera module (hereinafter referred to as the module for convenience of description) are as follows:
[0023] Step 1: Loosen the gripper of the six-axis robot, use the motion mechanism to send the lens of the module to the middle of the gripper of the six-axis robot, close the gripper, clamp the lens, and use the PLC motion control mechanism to send the sensor chip to the gripper of the six-axis robot Below the claw, the robot adjusts the lens to the initial adjustment position above the sensor chip;
[0024] Step 2: Trigger the module at the initial adjustment position or the adjusted new position to take the target image photo P1, adjust the Z axis of the robot to move it down the distance Zx (x=1,2,3,...), trigger The module takes the phot...
PUM
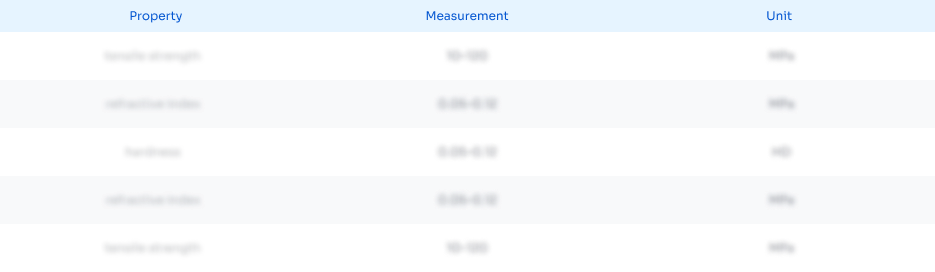
Abstract
Description
Claims
Application Information

- R&D Engineer
- R&D Manager
- IP Professional
- Industry Leading Data Capabilities
- Powerful AI technology
- Patent DNA Extraction
Browse by: Latest US Patents, China's latest patents, Technical Efficacy Thesaurus, Application Domain, Technology Topic, Popular Technical Reports.
© 2024 PatSnap. All rights reserved.Legal|Privacy policy|Modern Slavery Act Transparency Statement|Sitemap|About US| Contact US: help@patsnap.com