Preparation method for producing potassium calcium silicon magnesium fertilizer calcining fluxing agent
A technology of flux and calcination, which is applied in the direction of potash fertilizer, calcium fertilizer, application, etc., can solve the problem of small tolerance of raw material ingredients, and achieve the effect of solving difficult ingredients, improving heat utilization rate, and mineral utilization rate
- Summary
- Abstract
- Description
- Claims
- Application Information
AI Technical Summary
Problems solved by technology
Method used
Image
Examples
Embodiment 1
[0027] Example 1, such as figure 1 , figure 2 Shown:
[0028] Potassium feldspar, limestone or dolomite, and flux are used as raw materials, which are sequentially processed, crushed, stored, batched, pulverized, and calcined. Crushing: Among them, potassium feldspar, limestone or dolomite are generally in the form of blocks and need to be crushed and stored after crushing. The flux is generally in powder form and stored directly. Storage: Store raw materials and flux separately in the raw material warehouse or in the silo. Ingredients: According to the ratio, the raw materials and flux are individually weighed and fed, and then pulverized after aggregation. Grinding: The raw materials and the flux are finely ground and mixed together in the grinding process. The fineness of the finished grinding is 0.08mm. They are selected by the powder classifier and enter the powder warehouse. Calcination: The mixed powder enters the kiln for calcination, the temperature of the sinter...
Embodiment 2
[0040] Example 2, such as figure 1 , image 3 Shown:
[0041]Potassium feldspar and limestone or dolomite are used as raw materials, which are sequentially processed, crushed, stored, batched, ground, homogenized with flux, and calcined. 2. Crushing: Potassium feldspar, limestone or dolomite are generally in block shape and need to be crushed and stored after crushing. The flux is generally in powder form and stored directly. 1. Storage: Store raw materials and flux separately in the raw material warehouse or in the silo. 1. Ingredients: According to the ratio, the raw materials are individually weighed and fed, and then pulverized after aggregation. , Grinding: The raw materials are finely ground and mixed during the grinding process, and the fineness of the grinding is 0.08mm, and they are selected by the powder classifier and enter the homogenization warehouse. Homogenization with fluxing agent: measure when the raw material powder enters the homogenization storehouse, ...
PUM
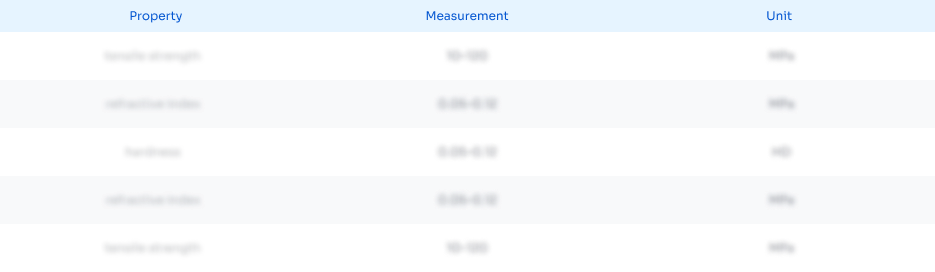
Abstract
Description
Claims
Application Information

- R&D
- Intellectual Property
- Life Sciences
- Materials
- Tech Scout
- Unparalleled Data Quality
- Higher Quality Content
- 60% Fewer Hallucinations
Browse by: Latest US Patents, China's latest patents, Technical Efficacy Thesaurus, Application Domain, Technology Topic, Popular Technical Reports.
© 2025 PatSnap. All rights reserved.Legal|Privacy policy|Modern Slavery Act Transparency Statement|Sitemap|About US| Contact US: help@patsnap.com