A kind of preparation method of laminated sound insulation material
A sound insulation material and a technology for preparation steps are applied in the field of preparation of laminated sound insulation materials, which can solve the problems of low sound insulation and achieve the effects of improving viscous resistance, improving sound absorption performance and good damping effect.
- Summary
- Abstract
- Description
- Claims
- Application Information
AI Technical Summary
Problems solved by technology
Method used
Image
Examples
example 1
[0028] Take 80g of nitrile rubber, 3g of zinc oxide, 1g of stearic acid, and 1g of anti-aging agent H, and add them into the torque rheometer for mixing for 8 minutes. The temperature is controlled at 120°C and the speed is 80r / min. Dioctyl phthalate, 1g sublimed sulfur, continue to mix for 8min, cool to room temperature to get the mixed rubber, place the mixed rubber on a flat vulcanizer, preheat at 120°C for 15min, then heat at 160°C, 8MPa Molded and vulcanized for 10 minutes, taken out and made into a sheet with a thickness of 3 mm, and cooled to room temperature to obtain a damping rubber. Take 20 g of titanate coupling agent and 50 g of silane coupling agent and add it to 1.0 L of deionized water. Stir at 300r / min for 3 hours, add 500g of acetone after cooling to room temperature, and put it into a centrifuge for centrifugation, take the upper layer solution to distill under reduced pressure to remove acetone, and obtain a macromolecular coupling agent, take 50g of macromo...
example 2
[0030]Take 90g of nitrile rubber, 4g of zinc oxide, 1g of stearic acid, and 2g of antioxidant H, and add them into a torque rheometer for mixing for 10 minutes. The temperature is controlled at 140°C, and the speed is 90r / min. Dioctyl phthalate, 1g sublimated sulfur, continue mixing for 10min, cool to room temperature to get the mixed rubber, put the mixed rubber on a flat vulcanizer, preheat at 130°C for 20min, and then heat it at 170°C, 10MPa Molded and vulcanized for 12 minutes, taken out and made into a sheet with a thickness of 4mm, and cooled to room temperature to obtain a damping rubber. Take 35g of titanate coupling agent and 65g of silane coupling agent and add it to 1.1L of deionized water. Stir at 350r / min for 3 hours, add 550g of acetone after cooling to room temperature, and put it into a centrifuge for centrifugation, take the upper layer solution to distill under reduced pressure to remove acetone, and obtain a macromolecular coupling agent, take 65g of macromol...
example 3
[0032] Take 100g of nitrile rubber, 5g of zinc oxide, 2g of stearic acid, and 3g of antioxidant H, and add them into a torque rheometer for mixing for 12 minutes. Dioctyl phthalate, 2g sublimated sulfur, continue mixing for 12min, cool to room temperature to get the mixed rubber, place the mixed rubber on a flat vulcanizer, preheat at 140°C for 25min, and then heat it at 180°C, 12MPa Molded and vulcanized for 15 minutes, taken out and made into a sheet with a thickness of 5mm, and cooled to room temperature to obtain a damping rubber. Take 50g of titanate coupling agent and 80g of silane coupling agent and add it to 1.2L of deionized water. Stir at 400r / min for 4 hours, add 600g of acetone after cooling to room temperature, and put it into a centrifuge for centrifugation, take the upper layer solution to distill under reduced pressure to remove acetone, and obtain a macromolecular coupling agent, take 80g of macromolecular coupling agent, 400g of silicic acid Add ethyl ester t...
PUM
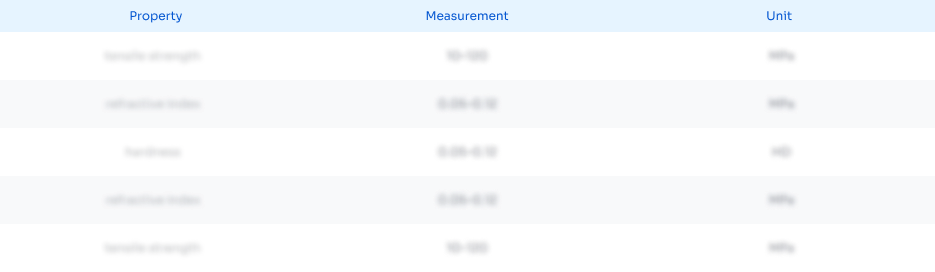
Abstract
Description
Claims
Application Information

- Generate Ideas
- Intellectual Property
- Life Sciences
- Materials
- Tech Scout
- Unparalleled Data Quality
- Higher Quality Content
- 60% Fewer Hallucinations
Browse by: Latest US Patents, China's latest patents, Technical Efficacy Thesaurus, Application Domain, Technology Topic, Popular Technical Reports.
© 2025 PatSnap. All rights reserved.Legal|Privacy policy|Modern Slavery Act Transparency Statement|Sitemap|About US| Contact US: help@patsnap.com