Edge error control method in optical lens small grinding head optical machining
An optical lens and optical processing technology, which is applied in the field of optical parts processing, can solve the problems of increasing the cost of processing equipment and application range, difficult to control the processing quality of edge parts, and warping, so as to reduce polishing costs, reduce convergence difficulty, and improve processing efficiency effect
- Summary
- Abstract
- Description
- Claims
- Application Information
AI Technical Summary
Problems solved by technology
Method used
Image
Examples
Embodiment
[0037] The polishing process of this embodiment is carried out on a polishing equipment based on an industrial robot, and the process parameters are set as follows: the diameter of the small grinding head is 25mm, the applied pressure is 10N, the revolution speed is 119rpm, the rotation speed is 200rpm, and the composition of the polishing liquid is CeO 2 , the concentration is 10% w.t, the ambient temperature is 23°C, the test workpiece to be polished is a concave BK7 optical glass with a diameter of 200mm, the radius of curvature is 1500mm, and the path selection is an Archimedes spiral.
[0038] The workpiece is polished by the following methods:
[0039] 1. Detection of surface shape error distribution: use laser interferometer to detect the surface shape error of the workpiece to be polished, the results are as follows figure 1 shown;
[0040] 2. Surface shape adjustment: Use surface shape adjustment technology to fine-tune the measured surface shape. The value of parame...
PUM
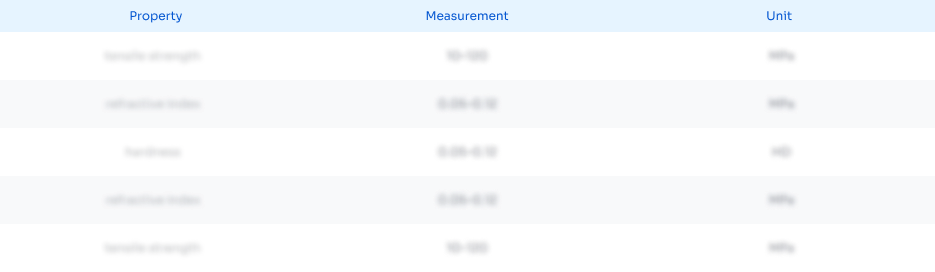
Abstract
Description
Claims
Application Information

- R&D Engineer
- R&D Manager
- IP Professional
- Industry Leading Data Capabilities
- Powerful AI technology
- Patent DNA Extraction
Browse by: Latest US Patents, China's latest patents, Technical Efficacy Thesaurus, Application Domain, Technology Topic, Popular Technical Reports.
© 2024 PatSnap. All rights reserved.Legal|Privacy policy|Modern Slavery Act Transparency Statement|Sitemap|About US| Contact US: help@patsnap.com