Physical system simulating molten metal droplet 3D printing in microgravity environment and printing method
A technology for simulating microgravity and metal droplets, applied in teaching models, instruments, additive processing, etc., which can solve problems such as expensive implementation time and unsuitable for early research on microdroplet 3D printing technology
- Summary
- Abstract
- Description
- Claims
- Application Information
AI Technical Summary
Problems solved by technology
Method used
Image
Examples
Embodiment 1
[0047] Method Example 1: In a gravity-free environment, that is, in an environment where the microgravity level is 0g (g is the gravitational acceleration on the earth's surface), the metal droplet deposition process is simulated.
[0048] Refer to attached figure 1 , 2 , the diameter of nozzle 2 is selected to be 50 μm, and the injection material is aerospace aluminum alloy (6061). The diameter of the metal droplet produced under this condition is also close to 50 μm, and the calculated Bond number of the metal droplet is 0.0013, which means that the gravity of the droplet ejection and deposition collision process has little influence on the flow field.
[0049] Calculate the Froude number of the droplet when the gravity is reduced to 10 -3 g~10 -5 g. From the definition of the Froude number, it can be seen that when the diameter of the metal droplet remains constant, the Froude number on the surface can be reduced by only accelerating the flight speed of the metal droplet...
Embodiment 2
[0052] Method Example 2: Simulation of the droplet printing process under different microgravity conditions (microgravity level kg, k is the microgravity proportional coefficient).
[0053] Refer to attached figure 1 , 2 , select the nozzle 2 with a diameter of 200 μm, add aerospace aluminum alloy (6061) into the metal droplet horizontal nozzle 1, heat and melt the metal material, and generate horizontally flying metal droplets 5 with a diameter of 200 μm through the function of the horizontal nozzle. After the metal droplet 5 flying horizontally is charged, the flying speed of the metal droplet is increased, so that the Froude number of the metal droplet on the surface is equal to the Froude number of the space droplet. The metal droplet flies through the initial vertical position detector 12, then continues to fly in the electrostatic field, and finally passes through the vertical position detector 10 when the metal droplet is deposited, and detects the offset distance of t...
PUM
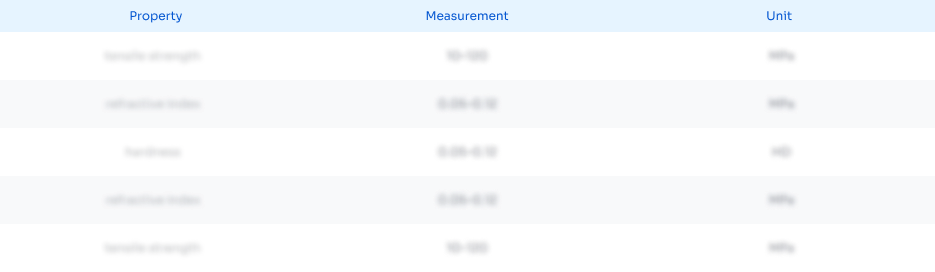
Abstract
Description
Claims
Application Information

- R&D
- Intellectual Property
- Life Sciences
- Materials
- Tech Scout
- Unparalleled Data Quality
- Higher Quality Content
- 60% Fewer Hallucinations
Browse by: Latest US Patents, China's latest patents, Technical Efficacy Thesaurus, Application Domain, Technology Topic, Popular Technical Reports.
© 2025 PatSnap. All rights reserved.Legal|Privacy policy|Modern Slavery Act Transparency Statement|Sitemap|About US| Contact US: help@patsnap.com