Pretreatment process of threshing and re-cured tobacco leaves based on characteristics of tobacco raw materials
A technology for threshing and redrying and pretreatment, which is applied in the field of threshing and redrying tobacco leaf pretreatment technology and the field of threshing and redrying pretreatment technology, can solve the problems of increased tobacco leaf fragmentation, high adhesion, and increased operating costs, etc. Achieve the effect of improving high adhesion and reducing the degree of fragmentation
- Summary
- Abstract
- Description
- Claims
- Application Information
AI Technical Summary
Problems solved by technology
Method used
Image
Examples
Embodiment 1
[0036] The tobacco leaf raw material in this example is the 2016 Fujian Nanping Central Tobacco Leaf.
[0037] ① Classification of Tobacco Leaf Raw Materials
[0038] Table 2 shows the detection results of the adhesion force of the tobacco leaf raw material and the moisture content of the tobacco leaf raw material in the cigarette pack in this embodiment. It can be seen from Table 2 that the adhesive force of the tobacco leaf raw material is 689.56g, and the moisture content of the tobacco leaf raw material in the cigarette pack is 16.58%. The tobacco leaf raw material can be classified as Class I-1 tobacco leaf.
[0039] Table 2 Test results of the adhesion of tobacco leaf raw materials and the moisture content of tobacco leaf raw materials in bales in this example
[0040] Tobacco Raw Materials Adhesion Moisture content of tobacco leaf raw materials in cigarette bales 2016 Fujian Nanping Central Tobacco Leaf 689.56 g 16.58%
[0041] ②Threshing and ...
Embodiment 2
[0049] The tobacco leaf raw material in this example is the upper part tobacco leaf of Xuchang, Henan in 2016.
[0050] ① Classification of Tobacco Leaf Raw Materials
[0051] Table 3 shows the test results of the adhesion force of the tobacco leaf raw material and the moisture content of the tobacco leaf raw material in the cigarette pack in this embodiment. It can be seen from Table 3 that the adhesive force of the tobacco leaf raw material is 385.26g, and the moisture content of the tobacco leaf raw material in the cigarette pack is 15.47%. The tobacco leaf raw material can be classified as Class II-2 tobacco leaf.
[0052] Table 3 The test results of the adhesion of tobacco leaf raw materials and the moisture content of tobacco leaf raw materials in bales in this example
[0053] Tobacco Raw Materials Adhesion Tobacco raw material moisture in cigarette bale 2016 Henan Xuchang Upper Tobacco Leaf 385.26 g 15.47%
[0054] ②Threshing and redrying pre...
PUM
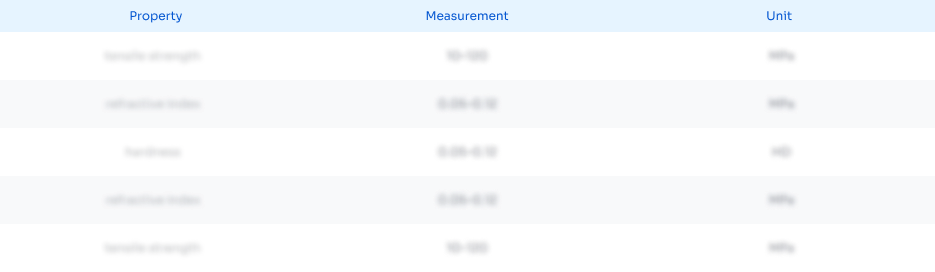
Abstract
Description
Claims
Application Information

- Generate Ideas
- Intellectual Property
- Life Sciences
- Materials
- Tech Scout
- Unparalleled Data Quality
- Higher Quality Content
- 60% Fewer Hallucinations
Browse by: Latest US Patents, China's latest patents, Technical Efficacy Thesaurus, Application Domain, Technology Topic, Popular Technical Reports.
© 2025 PatSnap. All rights reserved.Legal|Privacy policy|Modern Slavery Act Transparency Statement|Sitemap|About US| Contact US: help@patsnap.com