Method for recovering valuable metal from waste power battery cathode waste material
A power battery and valuable metal technology, applied in battery recycling, waste collector recycling, recycling technology, etc., can solve the problems of poor quality of lithium salt products, shorten the recovery process, short processing process, etc., and achieve easy industrialization Promote and avoid a large amount of high-sodium wastewater and the effect of high yield of valuable metals
- Summary
- Abstract
- Description
- Claims
- Application Information
AI Technical Summary
Problems solved by technology
Method used
Image
Examples
Embodiment 1
[0036] A method of the present invention for recovering valuable metals from waste ternary battery positive electrode waste provided by a battery factory in Hunan (positive electrode active waste obtained after safe discharge, physical disassembly, separation of aluminum foil, separation of conductive agent and binder) method, its process flow chart is as figure 1 shown, including the following steps:
[0037] (1) Add sulfuric acid and hydrogen peroxide to the positive electrode waste of this waste ternary battery for synergistic leaching treatment to obtain a nickel-cobalt-manganese-containing lithium leaching solution, and its composition is as shown in Table 1;
[0038] (2) Add lithium hydroxide to the nickel-cobalt-manganese-containing lithium leaching solution, adjust the pH of the solution to 4.8, and precipitate Fe, Al, and Cu in the form of hydroxides, and obtain impurity-removing residue and nickel-cobalt-manganese-containing lithium through solid-liquid separation P...
Embodiment 2
[0048] A method of the present invention for recovering valuable metals from waste ternary battery positive electrode waste provided by a battery factory in Changsha (positive electrode active waste obtained after safe discharge, physical disassembly, separation of aluminum foil, separation of conductive agent and binder) method, including the following steps:
[0049] (1) carry out acid leaching in this spent ternary battery positive electrode waste material, obtain containing nickel cobalt manganese lithium leaching solution, its composition is as shown in table 2;
[0050] (2) Add the sulfuric acid solution produced in step (6) in Example 1 to the nickel-cobalt-manganese lithium leaching solution, adjust the pH of the solution=2.5, and use the concentrated mother liquor saponification process produced in Example 1 step (7) P204 Carry out extraction deep impurity removal, make Fe, Al, Cu enter organic phase and separate and remove, obtain impurity removal liquid and nickel-c...
Embodiment 3
[0060] A kind of waste lithium cobalt oxide and lithium manganate battery positive electrode waste (positive electrode active waste obtained after safe discharge, physical disassembly, separation of aluminum foil, separation of conductive agent and binder) provided by a certain battery factory in Jiangxi according to the present invention A method for recovering valuable metals, comprising the steps of:
[0061] (1) carry out acid leaching treatment to this positive electrode waste material of battery and obtain lithium leaching solution containing nickel, cobalt, manganese, and its composition is as shown in table 3;
[0062] (2) Add the LiOH solution produced by step (6) in Example 2 to the nickel-cobalt-manganese-lithium leaching solution, adjust the pH of the solution=4.6, and make Fe, Al, and Cu precipitate in the form of hydroxides, and obtain the decomposed solution through solid-liquid separation. Miscellaneous slag and nickel-cobalt-manganese-lithium purification solu...
PUM
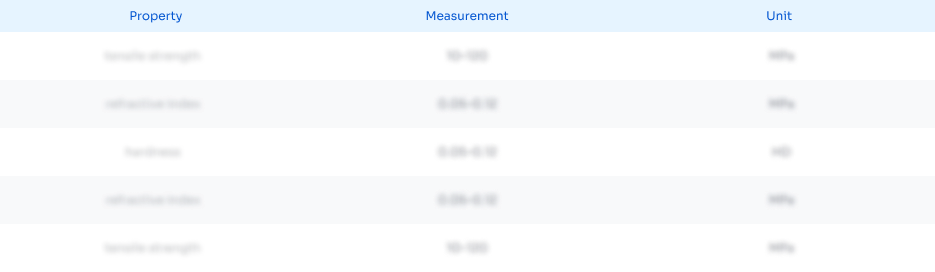
Abstract
Description
Claims
Application Information

- Generate Ideas
- Intellectual Property
- Life Sciences
- Materials
- Tech Scout
- Unparalleled Data Quality
- Higher Quality Content
- 60% Fewer Hallucinations
Browse by: Latest US Patents, China's latest patents, Technical Efficacy Thesaurus, Application Domain, Technology Topic, Popular Technical Reports.
© 2025 PatSnap. All rights reserved.Legal|Privacy policy|Modern Slavery Act Transparency Statement|Sitemap|About US| Contact US: help@patsnap.com