Treatment method of oxygen reduction and stopping of blast furnace in heavy-load and high oxygen enriched smelting
A heavy-duty blast furnace technology, applied in the field of blast furnace smelting, can solve problems such as abnormal furnace conditions, unstable gas flow, and increased bosh gas volume
- Summary
- Abstract
- Description
- Claims
- Application Information
AI Technical Summary
Problems solved by technology
Method used
Image
Examples
Embodiment Construction
[0041] In order to enable those skilled in the technical field to which the application belongs to understand the application more clearly, the technical solutions of the application will be described in detail below through specific embodiments in conjunction with the accompanying drawings.
[0042] The invention discloses a treatment method for reducing and stopping oxygen in heavy-duty high-oxygen smelting of a blast furnace.
[0043] see figure 1 , the method includes:
[0044] Step 11, detecting the oxygen reduction range in the blast furnace in real time.
[0045] Step 12, if the oxygen reduction range is greater than the preset oxygen reduction range threshold, perform the following steps.
[0046] Specifically, when there is a sudden and large oxygen reduction, the control of blast humidity, blast temperature and blast volume; the control of coke load and smelting intensity; the control of blast furnace coal injection amount; the control of furnace temperature and ga...
PUM
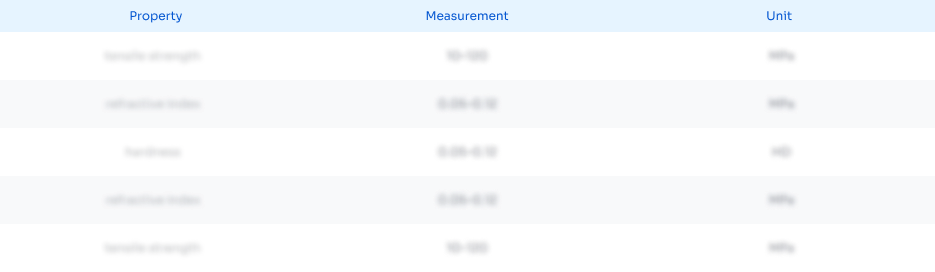
Abstract
Description
Claims
Application Information

- R&D
- Intellectual Property
- Life Sciences
- Materials
- Tech Scout
- Unparalleled Data Quality
- Higher Quality Content
- 60% Fewer Hallucinations
Browse by: Latest US Patents, China's latest patents, Technical Efficacy Thesaurus, Application Domain, Technology Topic, Popular Technical Reports.
© 2025 PatSnap. All rights reserved.Legal|Privacy policy|Modern Slavery Act Transparency Statement|Sitemap|About US| Contact US: help@patsnap.com