Multi-station automatic workpiece punching method
A multi-station, workpiece technology, applied in the field of stamping, can solve the problems of reducing stamping efficiency and low production efficiency, and achieve the effect of improving stamping efficiency and reducing labor intensity
- Summary
- Abstract
- Description
- Claims
- Application Information
AI Technical Summary
Problems solved by technology
Method used
Image
Examples
Embodiment Construction
[0020] The present invention will be further described in detail below in conjunction with the accompanying drawings and embodiments.
[0021] Such as figure 1 , 2 As shown, firstly, the multi-station automatic stamping device involved in this implementation will be described, which includes a feeding assembly 2 , a stamping assembly 3 and a rotary column assembly 1 .
[0022] Wherein, the feeding assembly 2 is located at the top, the stamping assembly 3 is located at the bottom, and the rotating column assembly 1 is arranged between the feeding assembly 2 and the stamping assembly 3 . The rotary column assembly 1 includes a central guide column 13, a rotary column 11 that is rotatably arranged on the central guide column 13, and a plurality of female molds 12 are arranged at circumferential intervals on the outer surface of the rotary column 11. After the shape of the workpiece is adapted, an electromagnet and an air pump are arranged on the rear side of each female mold 12...
PUM
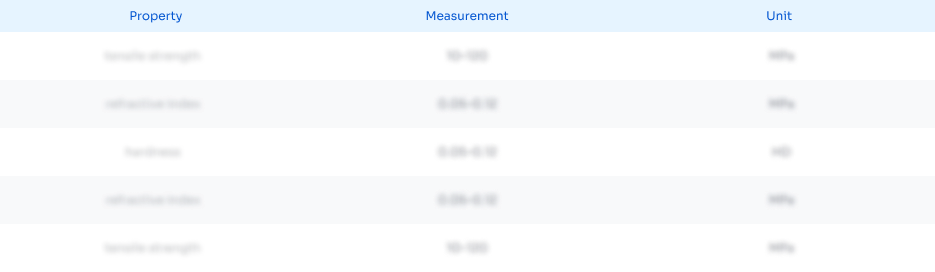
Abstract
Description
Claims
Application Information

- R&D
- Intellectual Property
- Life Sciences
- Materials
- Tech Scout
- Unparalleled Data Quality
- Higher Quality Content
- 60% Fewer Hallucinations
Browse by: Latest US Patents, China's latest patents, Technical Efficacy Thesaurus, Application Domain, Technology Topic, Popular Technical Reports.
© 2025 PatSnap. All rights reserved.Legal|Privacy policy|Modern Slavery Act Transparency Statement|Sitemap|About US| Contact US: help@patsnap.com