Sine wave power supply double-freedom-degree spiral motor with position self-locking function
A sine wave, degree of freedom technology, applied in the field of sine wave power supply dual-degree-of-freedom helical motor, can solve the problems of limiting the linear force and efficiency of the motor, the inability to use sine wave power supply, and the complex structure of the motor to achieve the effect of improving flexibility
- Summary
- Abstract
- Description
- Claims
- Application Information
AI Technical Summary
Problems solved by technology
Method used
Image
Examples
Embodiment Construction
[0030] The present invention will be further described below in conjunction with the accompanying drawings.
[0031] Such as figure 1 and figure 2 As shown, the sine wave power supply dual-degree-of-freedom spiral motor with position self-locking function of the present invention includes a stator core 1, an armature winding 2, a mover non-magnetic base 3, a mover magnetic core 4, and a rotating shaft 5; Iron core 1 is composed of stator power iron core 10 and stator annular iron core 11, and armature winding 2 is placed on stator power iron core 10; stator power iron core 10 and stator annular iron core 11 are arranged alternately and closely arranged along the axial direction; It is located on the non-magnetic base 3 of the mover; the non-magnetic base 3 of the mover, the magnetic core 4 of the mover and the rotating shaft 5 together constitute the mover.
[0032] Such as image 3 As shown, the mover presents a salient pole structure in the axial direction; the armature ...
PUM
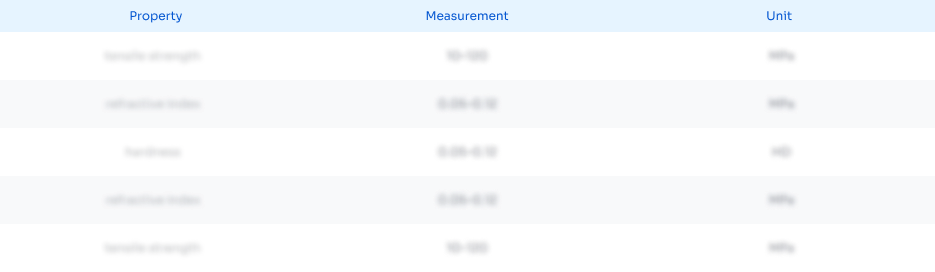
Abstract
Description
Claims
Application Information

- Generate Ideas
- Intellectual Property
- Life Sciences
- Materials
- Tech Scout
- Unparalleled Data Quality
- Higher Quality Content
- 60% Fewer Hallucinations
Browse by: Latest US Patents, China's latest patents, Technical Efficacy Thesaurus, Application Domain, Technology Topic, Popular Technical Reports.
© 2025 PatSnap. All rights reserved.Legal|Privacy policy|Modern Slavery Act Transparency Statement|Sitemap|About US| Contact US: help@patsnap.com