Composite wing optimization design method based on aerodynamic reduced-order model
A reduced-order model, composite material technology, applied in design optimization/simulation, calculation, special data processing applications, etc., can solve the problems of not considering airfoil camber and thickness, low aerodynamic accuracy, etc., to improve efficiency, improve The effect of accuracy
- Summary
- Abstract
- Description
- Claims
- Application Information
AI Technical Summary
Benefits of technology
Problems solved by technology
Method used
Image
Examples
Embodiment Construction
[0021] The present invention will be further described in detail with reference to the accompanying drawings and embodiments.
[0022] figure 1 These are the overall steps of the composite material wing optimization design method based on the aerodynamic reduced-order model of the present invention, and each implementation step is described in detail below.
[0023] Step 1: Establish the structural finite element model of the initial reference wing (ie, the initial reference model), and obtain the mode Φ of the structural model through modal analysis, including the frequency and mode shape of the mode.
[0024] Step 2, use CFD to calculate the aerodynamic force, and establish the aerodynamic model of the initial reference model. The modal Φ of the finite element model of the reference model is used, and the step signals of the mode shapes of each order are taken as input to obtain the aerodynamic response in the corresponding mode.
[0025] As it is done in the step response...
PUM
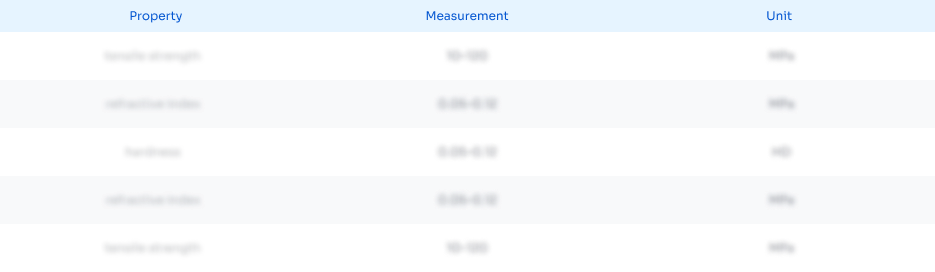
Abstract
Description
Claims
Application Information

- Generate Ideas
- Intellectual Property
- Life Sciences
- Materials
- Tech Scout
- Unparalleled Data Quality
- Higher Quality Content
- 60% Fewer Hallucinations
Browse by: Latest US Patents, China's latest patents, Technical Efficacy Thesaurus, Application Domain, Technology Topic, Popular Technical Reports.
© 2025 PatSnap. All rights reserved.Legal|Privacy policy|Modern Slavery Act Transparency Statement|Sitemap|About US| Contact US: help@patsnap.com