Regenerating method of waste thionyl chloride
A technology of thionyl chloride and polyacrylamide, which is applied in the field of purification of thionyl chloride and regeneration of waste thionyl chloride, can solve the problem of complex thionyl chloride composition, high investment in rectification equipment, and energy consumption of rectification process High-level problems, to achieve the effect of fast adsorption speed, low investment and low consumption
- Summary
- Abstract
- Description
- Claims
- Application Information
AI Technical Summary
Problems solved by technology
Method used
Examples
Embodiment 1
[0019] Embodiment 1: a kind of regeneration method of waste sulfur oxychloride, it comprises the steps:
[0020] Weigh 5g of anionic polyacrylamide and 5g of mordenite in the presence of 0.3g of silane coupling agent KH550 to prepare polyacrylamide / zeolite cross-linked composite adsorption material; The waste thionyl chloride produced by the acyl chloride production process was placed in a 100mL agitator, mixed evenly, and adsorbed for 60 minutes; vacuum distillation was carried out at 78°C to obtain 99.6% of the first-grade product thionyl chloride, with a recovery rate of 90% %.
Embodiment 2
[0021] Embodiment 2: a kind of regeneration method of waste sulfur oxychloride, it comprises the steps:
[0022] Weigh 150g of cationic polyacrylamide and 300g of beta zeolite in the presence of 4.5g of silane coupling agent KH570 to prepare cationic polyacrylamide / zeolite cross-linked composite adsorbent material. The waste thionyl chloride was placed in a 50L stirrer, mixed evenly, adsorbed for 90 minutes, and subjected to vacuum distillation at 78°C to obtain 99.7% first-grade thionyl chloride with a recovery rate of 98%.
Embodiment 3
[0023] Embodiment 3: a kind of regeneration method of waste sulfur oxychloride, it comprises the steps:
[0024] Weigh 5kg of cationic polyacrylamide and 10kg of beta zeolite in the presence of 150g of silane coupling agent KH550 to prepare cationic polyacrylamide / zeolite cross-linked composite adsorbent material. The waste thionyl chloride produced by chemical production process was placed in a 10 cubic meter agitator to make it evenly mixed, adsorbed for 120 minutes, and carried out vacuum distillation at 78°C to obtain 99.8% first-grade product thionyl chloride, the recovery rate 99%.
PUM
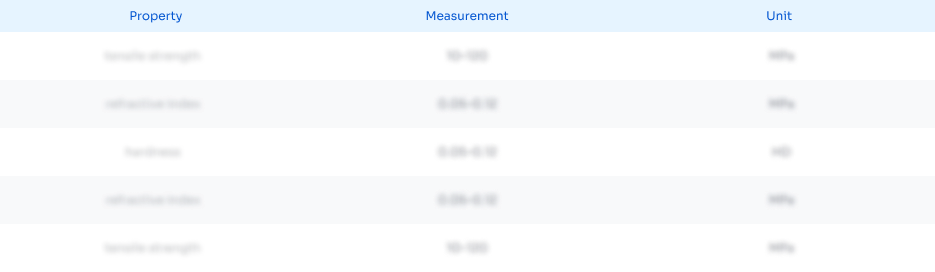
Abstract
Description
Claims
Application Information

- R&D
- Intellectual Property
- Life Sciences
- Materials
- Tech Scout
- Unparalleled Data Quality
- Higher Quality Content
- 60% Fewer Hallucinations
Browse by: Latest US Patents, China's latest patents, Technical Efficacy Thesaurus, Application Domain, Technology Topic, Popular Technical Reports.
© 2025 PatSnap. All rights reserved.Legal|Privacy policy|Modern Slavery Act Transparency Statement|Sitemap|About US| Contact US: help@patsnap.com