Rotor flux-based rotating speed calculation algorithm
A technology of rotor flux linkage and calculation algorithm, which is applied in the direction of electronically commutated motor control, generator control, control system, etc., can solve the problems of poor flux orientation accuracy, increased system hardware cost, and DC drift, etc., to achieve improved Accuracy, effect of improving observation results
- Summary
- Abstract
- Description
- Claims
- Application Information
AI Technical Summary
Problems solved by technology
Method used
Image
Examples
Embodiment Construction
[0025] In order to make the technical means, creative features, goals and effects of the present invention easy to understand, the following embodiments will specifically illustrate the rotor flux-linkage-based rotational speed calculation algorithm of the present invention in conjunction with the accompanying drawings.
[0026] figure 1 It is a schematic diagram of the improved current rotor flux linkage algorithm in the embodiment of the present invention.
[0027] The calculation algorithm of the rotational speed based on the rotor flux linkage in this embodiment includes the following steps:
[0028] Step 1: After calculating the stator voltage, the product of stator resistance and stator current, and the stator inductance L s Stator inductance i s The product is subtracted to obtain the calculated value of the rotor flux linkage on the stationary two-phase coordinates.
[0029]
[0030] ψ r is the rotor flux linkage, u s is the stator voltage vector, i s is the s...
PUM
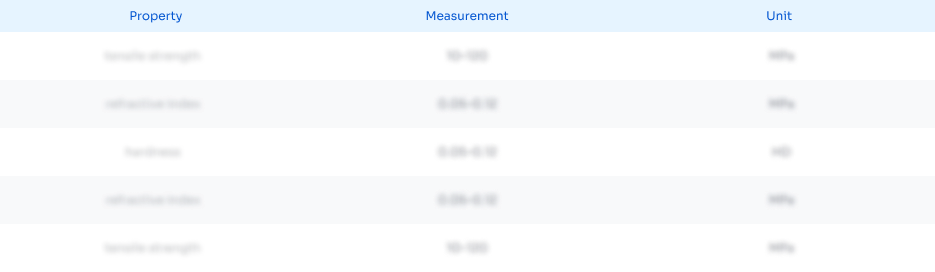
Abstract
Description
Claims
Application Information

- R&D
- Intellectual Property
- Life Sciences
- Materials
- Tech Scout
- Unparalleled Data Quality
- Higher Quality Content
- 60% Fewer Hallucinations
Browse by: Latest US Patents, China's latest patents, Technical Efficacy Thesaurus, Application Domain, Technology Topic, Popular Technical Reports.
© 2025 PatSnap. All rights reserved.Legal|Privacy policy|Modern Slavery Act Transparency Statement|Sitemap|About US| Contact US: help@patsnap.com