Dark green thermal resistance material as well as preparation method and application thereof
A dark green, thermal resistance technology, applied in epoxy resin coatings, coatings, etc., can solve the problems of inconvenient construction and unsatisfactory cooling effect, and achieve the effect of simple operation and suitable for large-scale production
- Summary
- Abstract
- Description
- Claims
- Application Information
AI Technical Summary
Problems solved by technology
Method used
Examples
preparation example Construction
[0046] The present invention provides a preparation method of the dark green thermal resistance material described in the above technical solution, comprising the following steps:
[0047] mixing epoxy resin, pigments and fillers with some diluents to obtain the first slurry;
[0048] Mixing the first slurry with dark green colored fillers and film-forming aids to obtain a second slurry;
[0049] The second slurry is mixed with the polyamide curing agent and the remaining diluent to obtain a dark green thermal resistance material.
[0050] In the present invention, epoxy resin, pigment and filler are mixed with part of diluent to obtain the first slurry. In the present invention, the mixing of the epoxy resin, pigments and fillers and part of the diluent is preferably to mix the epoxy resin and the pigments and fillers, stir at 50-70 rpm for 2-4 minutes, and then add part of the diluent to the resulting mixture , and stirred at 50-70 rpm for 3-5 minutes to obtain the first s...
Embodiment 1
[0056] In parts by weight, mix 11 parts of diatomaceous earth, 28.1 parts of rutile titanium dioxide and 23 parts of E-51 epoxy resin, stir at 60 rpm for 3 minutes, then add 10 parts of acetone, and stir at 60 rpm for 4 minutes to obtain the a slurry;
[0057] In the first slurry, add 5 parts of iron oxide green and 0.9 part of iron oxide black, stir at 60rpm until the color is uniform; then add 0.6 part of film-forming aid (the film-forming aid comprises tributyl phosphate, Acrylic ester and TEGO Dispers740W wetting and dispersing agent, the mass ratio of described tributyl phosphate, acrylate and TEGO Dispers 740W wetting and dispersing agent is 2:3:3), stirred at 60rpm for 3min, obtained the second slurry;
[0058] Add 9 parts of 650 polyamide curing agent to the second slurry, stir at 60 rpm for 5 minutes, then add 13 parts of acetone, and stir at 60 rpm for 4 minutes to obtain a dark green thermal resistance material.
Embodiment 2
[0060] In parts by weight, mix 9 parts of diatomaceous earth, 26 parts of rutile titanium dioxide and 27 parts of E-51 epoxy resin, stir at 60 rpm for 3 minutes, then add 11 parts of acetone, and stir at 60 rpm for 4 minutes to obtain the a slurry;
[0061] Add 5.5 parts of iron oxide green and 0.8 part of iron oxide black in the first slurry, stir at 60rpm until the color is uniform; then add 0.6 part of film-forming aid (the film-forming aid comprises tributyl phosphate, Acrylic ester and TEGO Dispers740W wetting and dispersing agent, the mass ratio of described tributyl phosphate, acrylate and TEGO Dispers 740W wetting and dispersing agent is 2:3:3), stirred at 60rpm for 3min, obtained the second slurry;
[0062] Add 10 parts of 650 polyamide curing agent to the second slurry, stir at 60 rpm for 5 minutes, then add 11 parts of acetone, and stir at 60 rpm for 4 minutes to obtain a dark green thermal resistance material.
PUM
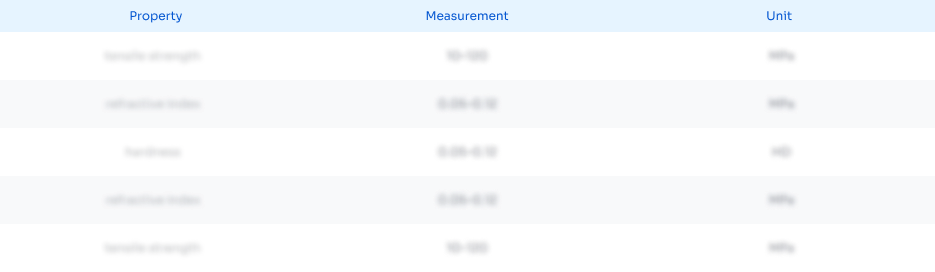
Abstract
Description
Claims
Application Information

- R&D
- Intellectual Property
- Life Sciences
- Materials
- Tech Scout
- Unparalleled Data Quality
- Higher Quality Content
- 60% Fewer Hallucinations
Browse by: Latest US Patents, China's latest patents, Technical Efficacy Thesaurus, Application Domain, Technology Topic, Popular Technical Reports.
© 2025 PatSnap. All rights reserved.Legal|Privacy policy|Modern Slavery Act Transparency Statement|Sitemap|About US| Contact US: help@patsnap.com