Preparation method of super-hydrophobic oleophylic polyurethane sponge
A Polyurethane Sponge, Hydrophilic Technology
- Summary
- Abstract
- Description
- Claims
- Application Information
AI Technical Summary
Problems solved by technology
Method used
Image
Examples
Embodiment 1
[0023] (1) Ultrasonic cleaning of 1ⅹ1ⅹ2cm polyurethane sponge in absolute ethanol for 30 minutes, take out and press out the ethanol in the sponge, then put it into acetone for ultrasonic cleaning for 30 minutes, and then press out the solvent in the cleaned sponge, Put it in an oven at 80°C for 60 minutes, and dry it for later use;
[0024] (2) Take waste tire tread rubber and ignite it with an alcohol lamp, grind the residue after burning into powder in a ball mill, the ball mill speed is 3800r / min, the grinding time is 1.5h, and pass through a 150-mesh standard inspection sieve; Add the sieved powder and 0.1g of polyvinyl formal resin adhesive to 50mL of acetone solvent, and stir for 10min to obtain a dispersion;
[0025] (3) Soak the dried polyurethane sponge in step (1) in the dispersion prepared in step (2), take it out after 2 minutes and place it in an oven at 100°C for 60 minutes to dry and solidify to obtain a superhydrophobic and lipophilic polyurethane sponge. The...
Embodiment 2
[0029] (1) Ultrasonic cleaning of 1ⅹ1ⅹ2cm polyurethane sponge in absolute ethanol for 20 minutes, take out and press out the ethanol, put it into acetone for ultrasonic cleaning for 20 minutes, then press out the solvent in the cleaned sponge, and place it in 100 ℃ oven for 40min, after drying for use;
[0030] (2) Take the waste tire tread rubber and ignite it with an alcohol lamp, and grind the burned residue into powder in a ball mill. Sieve powder and 0.08g butyl rubber adhesive, add to 45mL acetone solvent, stir for 15min to obtain dispersion;
[0031] (3) Soak the dried polyurethane sponge in step (1) in the dispersion prepared in step (2), take it out after 3 minutes and place it in an oven at 110°C for 50 minutes to dry and solidify to obtain a superhydrophobic and lipophilic polyurethane sponge. The contact angle of the test is shown in Table 1, and the absorption capacity is shown in Attached Table 2.
Embodiment 3
[0033] (1) Ultrasonic cleaning of 1ⅹ1ⅹ2cm polyurethane sponge in absolute ethanol for 25 minutes, take out and press out the ethanol, put the sponge in acetone for ultrasonic cleaning for 25 minutes, then press out the solvent in the cleaned sponge, and place Put it in an oven at 110°C for 25 minutes, and dry it for later use;
[0034] (2) Take waste tire tread rubber and ignite it with an alcohol lamp, and grind the burned residue into powder in a ball mill. Sieve the powder and 0.15g of polyurethane adhesive, add to 30mL of acetone solvent, stir for 18min to obtain a dispersion;
[0035] (3) Soak the dried polyurethane sponge in step (1) in the dispersion prepared in step (2), take it out after 5 minutes and place it in an oven at 90°C for 70 minutes to dry and solidify to obtain a superhydrophobic and lipophilic polyurethane sponge. The contact angle of the test is shown in Table 1, and the absorption capacity is shown in Attached Table 2.
[0036] Table 1 Surface contact...
PUM
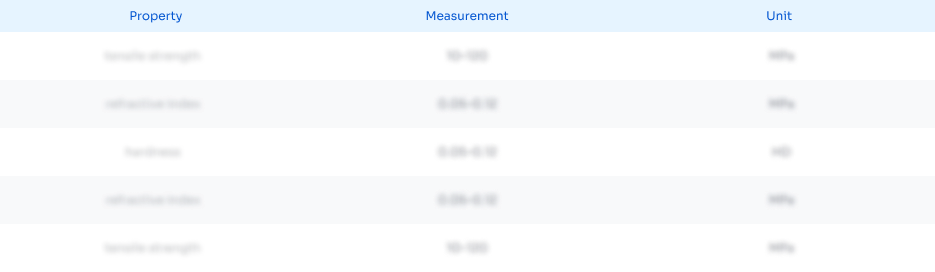
Abstract
Description
Claims
Application Information

- R&D
- Intellectual Property
- Life Sciences
- Materials
- Tech Scout
- Unparalleled Data Quality
- Higher Quality Content
- 60% Fewer Hallucinations
Browse by: Latest US Patents, China's latest patents, Technical Efficacy Thesaurus, Application Domain, Technology Topic, Popular Technical Reports.
© 2025 PatSnap. All rights reserved.Legal|Privacy policy|Modern Slavery Act Transparency Statement|Sitemap|About US| Contact US: help@patsnap.com