Energy consumption modeling and local energy consumption benchmarking method for horseshoe flame glass kiln
A glass kiln and horseshoe flame technology, applied in special data processing applications, instruments, electrical digital data processing, etc., can solve problems such as incomplete energy management, backward operating technology, and unreasonable insulation measures
- Summary
- Abstract
- Description
- Claims
- Application Information
AI Technical Summary
Problems solved by technology
Method used
Image
Examples
Embodiment 1
[0029] The energy consumption modeling and local energy consumption benchmarking method of the horseshoe flame glass kiln in this embodiment includes the following steps:
[0030] Step A, collect the production data of the horseshoe-flame glass kiln, and establish the combustion space energy consumption model, the melting tank energy consumption model and the regenerator energy consumption model respectively according to the material conservation and heat balance; step B, dissipate heat from the wall of the horseshoe-flame glass kiln The loss is divided into three major control body boundaries. The three major control body boundaries are composed of the combustion space roof and furnace wall, the melting tank bottom and pool wall, and the regenerator roof and wall, and the kiln wall heat loss model is established; Step C, by obtaining the energy consumption prediction data of the combustion space energy consumption model, the melting pool energy consumption model and the regene...
Embodiment 2
[0124] In this example, the glass kiln structure and operating process parameters of a glass factory in Guangdong and the collected on-site temperature and flow data are used as model input parameters to solve the energy consumption model of each key module in Example 1, and then calculate based on the energy consumption model The energy consumption forecast data of each cycle is used to establish the local energy consumption benchmark of the glass kiln, and then use the local energy consumption benchmark to achieve a detailed analysis of the details of the energy consumption of each module, and then obtain the minimum SEC of the glass kiln, and finally determine the energy consumption of the glass kiln. Local benchmark management analysis of energy consumption can be carried out to determine the unnecessary energy consumption of each module in each cycle of the entire glass kiln process production process, and provide theoretical basis and method support for guiding the actual ...
PUM
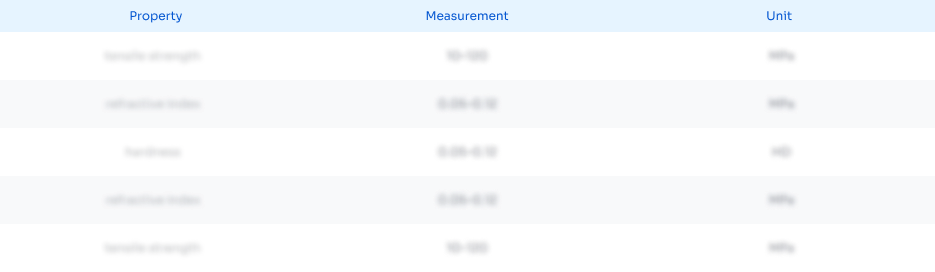
Abstract
Description
Claims
Application Information

- R&D Engineer
- R&D Manager
- IP Professional
- Industry Leading Data Capabilities
- Powerful AI technology
- Patent DNA Extraction
Browse by: Latest US Patents, China's latest patents, Technical Efficacy Thesaurus, Application Domain, Technology Topic, Popular Technical Reports.
© 2024 PatSnap. All rights reserved.Legal|Privacy policy|Modern Slavery Act Transparency Statement|Sitemap|About US| Contact US: help@patsnap.com