Method for producing high-purity cobalt chloride by utilizing cobalt carbonate defective products
A technology of cobalt chloride and cobalt carbonate, which is applied in chemical instruments and methods, cobalt halides, cobalt compounds, etc., can solve the problems of being unable to be directly acid-soluble and having no cost advantage, and achieves low production cost, high cobalt recovery rate, The effect of simple process
- Summary
- Abstract
- Description
- Claims
- Application Information
AI Technical Summary
Problems solved by technology
Method used
Examples
Embodiment 1
[0040] Embodiment 1: Utilize cobalt carbonate residual product to produce high-purity cobalt chloride
[0041] Weigh the residual cobalt carbonate and add water to the stirred reactor for slurrying. A 160 g / l hydrochloric acid solution was added to a final pH=1.5.
[0042] Cobalt carbonate was added to the resulting solution to reverse the pH to 3.5, and a cobalt chloride solution was obtained after pressure filtration.
[0043] Pour the above cobalt chloride solution into a heated and stirred reactor, raise the temperature to 85°C, and slowly add 40g / l sodium hydroxide solution to adjust the pH to 4.5-5.0 under the condition of sufficient stirring.
[0044] When the pH is completely stable at 4.5-5.0, slowly add ammonium fluoride with an excess coefficient of 1.1, and keep stirring for one hour. Co 2+ ≥100g / l, Fe 3+ ≤0.5ug / ml, Cu 2+ ≤0.5ug / ml, Al 3+ ≤0.5ug / ml, Mg 2+ The high-purity cobalt chloride solution of ≤5ug / ml can reach the battery grade standard, and the yield ...
Embodiment 2
[0045] Embodiment 2: Utilize cobalt carbonate residual product to produce high-purity cobalt chloride
[0046] Weigh the residual cobalt carbonate and add water to the stirred reactor for slurrying. And control the speed to add 175g / l hydrochloric acid solution to the final pH=1.
[0047] Add cobalt carbonate to the solution in step (1) to adjust the pH to 4.0, and press filter to obtain a cobalt chloride solution.
[0048] Put the above cobalt chloride solution into a heated and stirred reactor, raise the temperature to 80°C, and slowly add 40g / l sodium hydroxide solution to adjust the pH to 4.7 under the condition of sufficient stirring.
[0049] When the pH is completely stable above 4.5, slowly add ammonium fluoride with an excess coefficient of 1.2, and keep stirring for one and a half hours. After filtering to get Co 2+ ≥100g / l, Fe 3+ ≤0.5ug / ml, Cu 2+ ≤0.5ug / ml, Al 3+ ≤0.5ug / ml, Mg 2+ The high-purity cobalt chloride solution of ≤5ug / ml can reach the battery grade ...
Embodiment 3
[0050] Embodiment 3: Utilize cobalt carbonate residual product to produce high-purity cobalt chloride
[0051] Weigh the residual cobalt carbonate and add water to the stirred reactor for slurrying. And control the speed to add 190g / l hydrochloric acid solution to the final pH=2.
[0052] Add cobalt carbonate to the solution in step (1) to adjust the pH to 3.0, and obtain a cobalt chloride solution after pressure filtration.
[0053]Pour the above cobalt chloride solution into a heated and stirred reactor, raise the temperature to 90°C, and slowly add 40g / l sodium hydroxide solution to adjust the pH to 5 under the condition of sufficient stirring.
[0054] When the pH is completely stable above 4.5, slowly add ammonium fluoride with an excess coefficient of 1.5, and keep stirring for two hours. After filtering to get Co 2+ ≥100g / l, Fe 3+ ≤0.5ug / ml, Cu 2+ ≤0.5ug / ml, Al 3+ ≤0.5ug / ml, Mg 2+ The high-purity cobalt chloride solution of ≤5ug / ml can reach the battery grade sta...
PUM
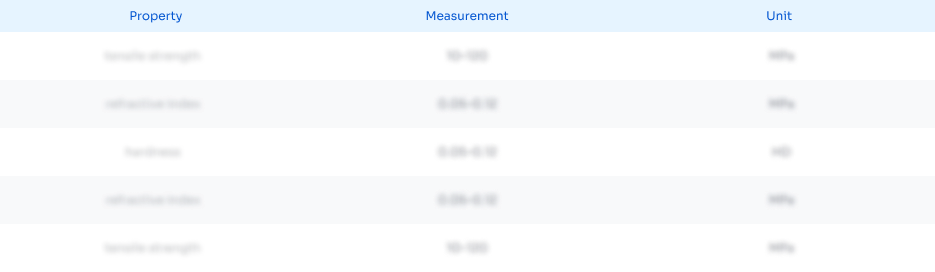
Abstract
Description
Claims
Application Information

- Generate Ideas
- Intellectual Property
- Life Sciences
- Materials
- Tech Scout
- Unparalleled Data Quality
- Higher Quality Content
- 60% Fewer Hallucinations
Browse by: Latest US Patents, China's latest patents, Technical Efficacy Thesaurus, Application Domain, Technology Topic, Popular Technical Reports.
© 2025 PatSnap. All rights reserved.Legal|Privacy policy|Modern Slavery Act Transparency Statement|Sitemap|About US| Contact US: help@patsnap.com