High-strength welding clamp surface treatment method
A welding fixture and surface treatment technology, applied in chemical instruments and methods, cleaning methods and utensils, cleaning methods using liquids, etc., can solve the inaccurate and stable shape and size of welding products, short service life, and inaccurate positioners and other issues, to achieve the effect of improving fatigue strength, prolonging safe working life and prolonging service life
- Summary
- Abstract
- Description
- Claims
- Application Information
AI Technical Summary
Problems solved by technology
Method used
Examples
Embodiment 1
[0015] A surface treatment method for a high-strength welding fixture, comprising the following steps:
[0016] (1) Sprinkle hydrochloric acid solution evenly on the surface of the welding fixture. After 10 minutes, wash the surface with clean water, and then evenly brush the surface of the welding fixture with the pre-peening liquid, wherein the pre-peening liquid is made of the following components by weight : 9 parts of sodium phosphate, 5 parts of ammonia water, 2 parts of benzyltrimethylammonium iodide, 1 part of sodium hexafluorophosphate, 4 parts of sodium polysulfide, 190 parts of water;
[0017] (2) Use a shot blasting machine to spray ceramic projectiles onto the surface of the welding fixture. The average diameter of the ceramic projectiles is 500 μm, the spray angle is 90°, and the distance from the nozzle to the sample is 180 mm.
[0018] Specifically, the volume fraction of the hydrochloric acid solution in the above step (1) is 7%.
[0019] Specifically, the me...
Embodiment 2
[0022] A surface treatment method for a high-strength welding fixture, comprising the following steps:
[0023] (1) Sprinkle hydrochloric acid solution evenly on the surface of the welding fixture. After 10 minutes, wash the surface with clean water, and then evenly brush the surface of the welding fixture with the pre-peening liquid, wherein the pre-peening liquid is made of the following components by weight : 11 parts of sodium phosphate, 6 parts of ammonia water, 3 parts of benzyltrimethylammonium iodide, 2 parts of sodium hexafluorophosphate, 5 parts of sodium polysulfide, 195 parts of water;
[0024] (2) Use a shot blasting machine to spray ceramic projectiles onto the surface of the welding fixture. The average diameter of the ceramic projectiles is 500 μm, the spray angle is 90°, and the distance from the nozzle to the sample is 180 mm.
[0025] Specifically, the volume fraction of the hydrochloric acid solution in the above step (1) is 7%.
[0026] Specifically, the ...
Embodiment 3
[0029] A surface treatment method for a high-strength welding fixture, comprising the following steps:
[0030] (1) Sprinkle hydrochloric acid solution evenly on the surface of the welding fixture. After 10 minutes, wash the surface with clean water, and then evenly brush the surface of the welding fixture with the pre-peening liquid, wherein the pre-peening liquid is made of the following components by weight : 13 parts of sodium phosphate, 7 parts of ammonia water, 4 parts of benzyltrimethylammonium iodide, 3 parts of sodium hexafluorophosphate, 6 parts of sodium polysulfide, 200 parts of water;
[0031] (2) Use a shot blasting machine to spray ceramic projectiles onto the surface of the welding fixture. The average diameter of the ceramic projectiles is 500 μm, the spray angle is 90°, and the distance from the nozzle to the sample is 180 mm.
[0032] Specifically, the volume fraction of the hydrochloric acid solution in the above step (1) is 7%.
[0033] Specifically, the ...
PUM
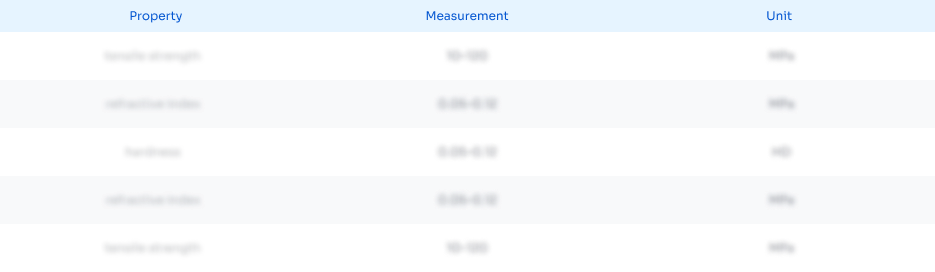
Abstract
Description
Claims
Application Information

- R&D
- Intellectual Property
- Life Sciences
- Materials
- Tech Scout
- Unparalleled Data Quality
- Higher Quality Content
- 60% Fewer Hallucinations
Browse by: Latest US Patents, China's latest patents, Technical Efficacy Thesaurus, Application Domain, Technology Topic, Popular Technical Reports.
© 2025 PatSnap. All rights reserved.Legal|Privacy policy|Modern Slavery Act Transparency Statement|Sitemap|About US| Contact US: help@patsnap.com