Silicon release agent and preparation method thereof
A technology of release agent and organic solvent, which is applied in the field of silicon release agent and its preparation, can solve the problems that cannot cover molded plastics, silicon release agent release performance, and insufficient anti-fouling performance, so as to achieve easy removal and easy release mod effect
- Summary
- Abstract
- Description
- Claims
- Application Information
AI Technical Summary
Problems solved by technology
Method used
Image
Examples
Embodiment 1
[0062] Preparation of Release Agent 1:
[0063] In a 500ml round-bottomed flask equipped with an electromagnetic stirrer, a condenser, a thermometer, and a nitrogen gas injection supply device, nitrogen gas (0.5 Ltr / min) was circulated slightly, a magnet was put in and stirring was started, and 13.0 grams of poly(dimethacrylate) containing methacrylate was dropped. Methylsiloxane, 0.52 g of 1,1,3,3-tetramethyl dihydrodisiloxane (1,1,3,3-Tetramethyl dihydrodisiloxane), 32.0 g of tetrahydrofuran and 230 g of n-heptane. Stirring was continued at room temperature for 10 minutes to form a homogeneous solution. Next, add 0.105 g of a platinum catalyst solution containing substituents, keep stirring at a temperature of 60-65°C for 40 minutes, then add 0.65 g of vinyltrimethoxysilane, and keep stirring at a temperature of 60-65°C for 40 minutes to form The addition product solution with siloxane and siloxane backbone is finally formulated to have a volatile content of 5%, and the ins...
Embodiment 2
[0065] Preparation of release agent 2:
[0066] In a 500ml round-bottomed flask equipped with an electromagnetic stirrer, condenser, thermometer, and nitrogen injection supply device, nitrogen gas (0.5 Ltr / min) was circulated slightly, a magnet was placed and stirring was started, and 10.5 grams of monovinyl polydimethylsilane was added Oxygen (Mono-vinyl terminated PDMS), 1.2 grams of terminal dihydrogen polysiloxane, 30 grams of tetrahydrofuran and 212 grams of n-heptane. Stirring was continued at room temperature for 10 minutes to form a homogeneous solution. Next, add 0.105 g of a platinum catalyst containing an organic substituent, stir at a temperature of 50-60°C for 40 minutes, then add 1.65 g of allyl trimethoxysilane, and keep the temperature at 60-65°C. Warm stirring for 40 minutes to form a silicon addition product solution, which was finally formulated to have a volatile content of 5%, was filtered through a 100 micron (micron) filter to remove insolubles, and obt...
Embodiment 3
[0068] Preparation of release agent 3:
[0069] In a 600ml round-bottomed flask equipped with an electromagnetic stirrer, condenser, thermometer, and nitrogen injection supply device, nitrogen gas (0.5 Ltr / min) was circulated slightly, a magnet was placed and stirring was started, and 24.0 grams of polydimethylmethacrylate containing base siloxane, 6.50 grams of terminal dihydrogen polysiloxane, 42 grams of tetrahydrofuran and 420 grams of n-heptane. Stirring was continued at room temperature for 10 minutes to form a homogeneous solution. Next, add 0.105 g of a platinum catalyst solution containing substituents, keep stirring at a temperature of 40 to 50°C for 40 minutes, and then add 1.00 g of 3-methacryloxy propyltrimethoxy -silane), kept warm and stirred at 60-65°C for 90 minutes to form an addition product solution with a backbone of siloxane and silane, and finally prepared a volatile content of 5%, passing through a 100 micron (micron) filter The insolubles were remove...
PUM
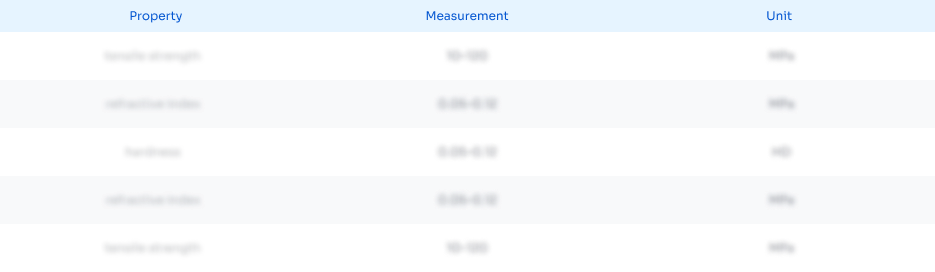
Abstract
Description
Claims
Application Information

- R&D Engineer
- R&D Manager
- IP Professional
- Industry Leading Data Capabilities
- Powerful AI technology
- Patent DNA Extraction
Browse by: Latest US Patents, China's latest patents, Technical Efficacy Thesaurus, Application Domain, Technology Topic, Popular Technical Reports.
© 2024 PatSnap. All rights reserved.Legal|Privacy policy|Modern Slavery Act Transparency Statement|Sitemap|About US| Contact US: help@patsnap.com