TFT manufacturing method and TFT substrate
A manufacturing method and substrate substrate technology, applied in semiconductor/solid-state device manufacturing, electrical components, electrical solid-state devices, etc., can solve problems affecting the characteristics of TFT devices, etc., and achieve the effect of avoiding etching residues
- Summary
- Abstract
- Description
- Claims
- Application Information
AI Technical Summary
Problems solved by technology
Method used
Image
Examples
Embodiment Construction
[0047] The following will clearly and completely describe the technical solutions of each exemplary embodiment provided by the present invention with reference to the accompanying drawings in the embodiments of the present invention. In the case of no conflict, the following embodiments and features in the embodiments can be combined with each other.
[0048] figure 2 It is a schematic flow chart of a manufacturing method of a TFT according to an embodiment of the present invention, image 3 is based on figure 2 Schematic diagram of the scenario of TFT fabrication by the shown method. combine figure 2 and image 3 As shown, the manufacturing method of the TFT includes the following steps S21-S29.
[0049] S21: Provide a base substrate.
[0050] The base substrate 30 may be a transparent substrate such as a glass substrate, a plastic substrate, or a flexible substrate.
[0051] S22: sequentially forming a gate pattern, a gate insulating layer and an amorphous silicon ...
PUM
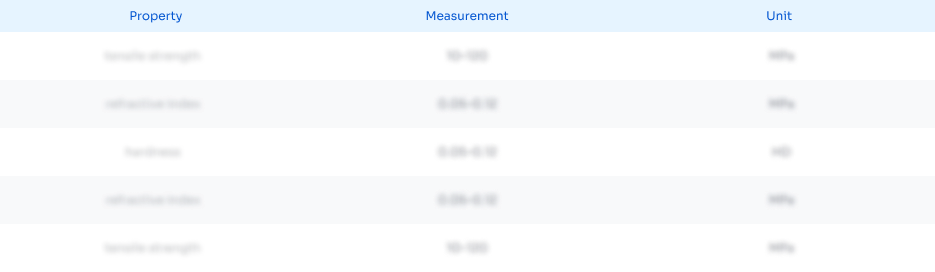
Abstract
Description
Claims
Application Information

- R&D Engineer
- R&D Manager
- IP Professional
- Industry Leading Data Capabilities
- Powerful AI technology
- Patent DNA Extraction
Browse by: Latest US Patents, China's latest patents, Technical Efficacy Thesaurus, Application Domain, Technology Topic, Popular Technical Reports.
© 2024 PatSnap. All rights reserved.Legal|Privacy policy|Modern Slavery Act Transparency Statement|Sitemap|About US| Contact US: help@patsnap.com