Preparation method of ultrafine panax notoginseng powder cellulosic fiber
A technology of cellulose fiber and ultra-fine Panax notoginseng powder, applied in the direction of cellulose/protein conjugated rayon, fiber chemical characteristics, rayon manufacturing, etc., can solve the problem of low burst strength and tensile strength, , high tearing degree, to achieve the effect of prolonging human lifespan, improving microcirculation, and improving immune function of the body
- Summary
- Abstract
- Description
- Claims
- Application Information
AI Technical Summary
Problems solved by technology
Method used
Examples
Embodiment 1
[0023] A method for preparing superfine notoginseng powder cellulose fiber, comprising the following process steps:
[0024] Step 1, pretreatment, by weight percentage, take 20% of notoginseng powder, add 2% of dispersant, add deionized water to 100%, fully mix and stir the mixed system to obtain the notoginseng powder dispersion;
[0025] In the second step, the spinning stock solution is prepared, the notoginseng powder dispersion prepared in the first step and a certain amount of bamboo pulp are fully mixed and stirred, and the binder is added to obtain the spinning stock solution;
[0026] In the 3rd step, the spinning stock solution obtained in the 2nd step is extruded from the spinneret hole to form a thin stream of the stock solution;
[0027] In the 4th step, the thin stream of the stock solution obtained in the 3rd step is coagulated into nascent fibers;
[0028] In step 5, the primary fiber is packaged or processed directly to obtain the finished product.
[0029] ...
Embodiment 2
[0034] A method for preparing superfine notoginseng powder cellulose fiber, comprising the following process steps:
[0035] Step 1, pretreatment, by weight percentage, take 50% of the notoginseng powder, add 10% of the dispersant, add deionized water to 100%, fully mix and stir the mixed system to obtain the notoginseng powder dispersion;
[0036] In the second step, the spinning stock solution is prepared, the notoginseng powder dispersion prepared in the first step and a certain amount of bamboo pulp are fully mixed and stirred, and the binder is added to obtain the spinning stock solution;
[0037] In the 3rd step, the spinning stock solution obtained in the 2nd step is extruded from the spinneret hole to form a thin stream of the stock solution;
[0038] In the 4th step, the thin stream of the stock solution obtained in the 3rd step is coagulated into nascent fibers;
[0039] In step 5, the primary fiber is packaged or processed directly to obtain the finished product. ...
Embodiment 3
[0045] A method for preparing superfine notoginseng powder cellulose fiber, comprising the following process steps:
[0046] Step 1, pretreatment, by weight percentage, take 35% of notoginseng powder, add 6% of dispersant, add deionized water to 100%, fully mix and stir the mixed system to obtain the notoginseng powder dispersion;
[0047] In the second step, the spinning stock solution is prepared, the notoginseng powder dispersion prepared in the first step and a certain amount of bamboo pulp are fully mixed and stirred, and the binder is added to obtain the spinning stock solution;
[0048] In the 3rd step, the spinning stock solution obtained in the 2nd step is extruded from the spinneret hole to form a thin stream of the stock solution;
[0049]In the 4th step, the thin stream of the stock solution obtained in the 3rd step is coagulated into nascent fibers;
[0050] In step 5, the primary fiber is packaged or processed directly to obtain the finished product.
[0051] I...
PUM
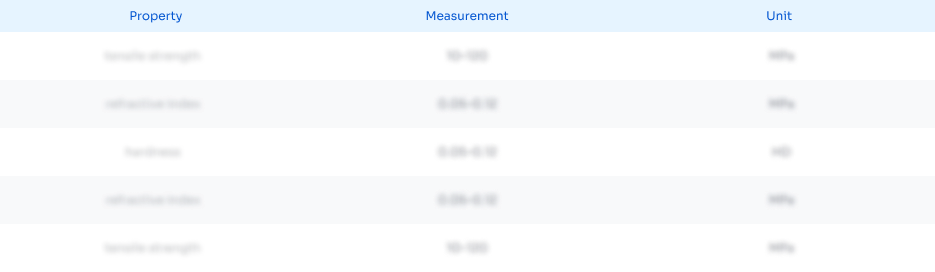
Abstract
Description
Claims
Application Information

- R&D
- Intellectual Property
- Life Sciences
- Materials
- Tech Scout
- Unparalleled Data Quality
- Higher Quality Content
- 60% Fewer Hallucinations
Browse by: Latest US Patents, China's latest patents, Technical Efficacy Thesaurus, Application Domain, Technology Topic, Popular Technical Reports.
© 2025 PatSnap. All rights reserved.Legal|Privacy policy|Modern Slavery Act Transparency Statement|Sitemap|About US| Contact US: help@patsnap.com