Integrated robot joint module
A technology of robot joints and joints, which is applied in the field of robots, can solve problems such as single working environment, low load-to-weight ratio, and lack of flexibility, and achieve the effects of optimizing the structure of the whole machine, saving structural space, and improving safety
- Summary
- Abstract
- Description
- Claims
- Application Information
AI Technical Summary
Problems solved by technology
Method used
Image
Examples
Embodiment Construction
[0035] In order to make the object, technical solution and advantages of the present invention clearer, the implementation manner of the present invention will be further described in detail below in conjunction with the accompanying drawings.
[0036] An integrated robot joint module, including joint output member 1, harmonic reducer 2, joint housing 3, drive motor body 4, brake mechanism 5, motor input encoder 6, joint output encoder 7, integrated circuit modules 8, such as figure 1 shown.
[0037]The joint output component 1 is used to connect the external actuator or load; the harmonic reducer 2 is used to adjust the rotation speed of the joint output component 1; the joint shell 3 is used to fix the harmonic reducer 2, the driving motor body 4, the brake mechanism 5, and the motor The input end encoder 6, the joint output end encoder 7 and the integrated circuit module 8; the drive motor main body 4 is used to drive the harmonic reducer 2 according to the instruction of ...
PUM
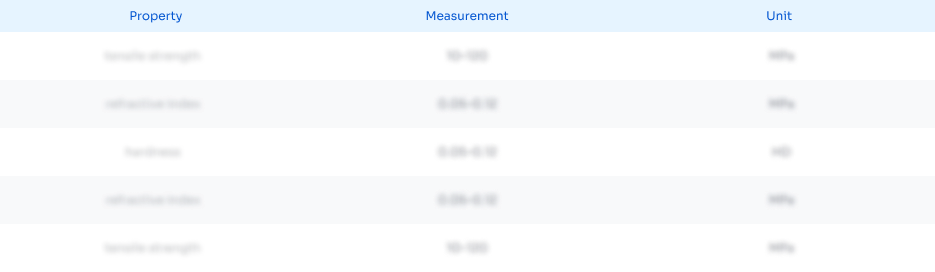
Abstract
Description
Claims
Application Information

- R&D
- Intellectual Property
- Life Sciences
- Materials
- Tech Scout
- Unparalleled Data Quality
- Higher Quality Content
- 60% Fewer Hallucinations
Browse by: Latest US Patents, China's latest patents, Technical Efficacy Thesaurus, Application Domain, Technology Topic, Popular Technical Reports.
© 2025 PatSnap. All rights reserved.Legal|Privacy policy|Modern Slavery Act Transparency Statement|Sitemap|About US| Contact US: help@patsnap.com