Forging method for improving flaw detection bottom losses of GH4169 alloy die forgings
A GH4169, die forging technology, applied in the field of forging hot processing, can solve the problems of waste of resources, excessive bottom loss, products can not meet the needs of users, etc., to achieve the effect of improving product yield
- Summary
- Abstract
- Description
- Claims
- Application Information
AI Technical Summary
Problems solved by technology
Method used
Image
Examples
specific Embodiment
[0030] For the high-pressure turbine rear axle described in the present invention, the size and shape of the forging are as follows: figure 2 ;Material: GH4169, category Ⅱ, process specification requires blanking specification: φ220×371, weight: 96Kg, the overall performance index of the forging and the low-damage requirements of flaw detection should meet the requirements of the Q / S10-0313 standard.
[0031] The forging steps are detailed as follows:
[0032] The first step: put the φ200×371mm billet into the electric furnace ≤700°C and heat it up to 850°C for 150 minutes, then heat it to 1010°C for 150 minutes at high temperature, and prefabricate the cake blank to H=170mm (completed by 1 fire), and the shape is as follows figure 1 ;
[0033] The second step: car prefabricated biscuit to H 1 =162mm;
[0034] The third step: the bottom damage inspection of flaw detection, according to the requirements of Q / S10-0313 standard;
[0035] Step 4: Put the inspected prefabricat...
PUM
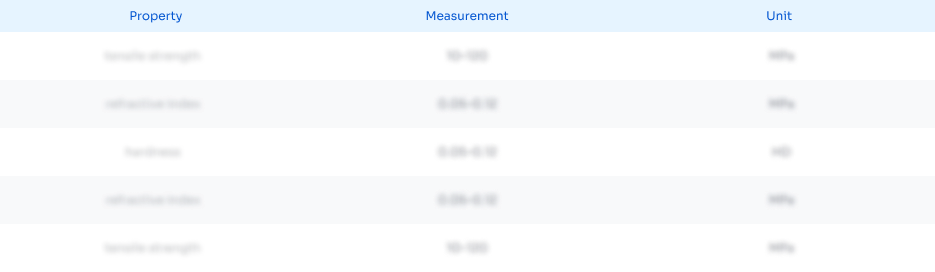
Abstract
Description
Claims
Application Information

- R&D
- Intellectual Property
- Life Sciences
- Materials
- Tech Scout
- Unparalleled Data Quality
- Higher Quality Content
- 60% Fewer Hallucinations
Browse by: Latest US Patents, China's latest patents, Technical Efficacy Thesaurus, Application Domain, Technology Topic, Popular Technical Reports.
© 2025 PatSnap. All rights reserved.Legal|Privacy policy|Modern Slavery Act Transparency Statement|Sitemap|About US| Contact US: help@patsnap.com