T-bed body split core method based on additive manufacturing
An additive manufacturing and material technology, applied in the direction of cores, mold components, manufacturing tools, etc., can solve the problems of difficult control of casting quality, difficult cleaning, and difficult to control the positioning size of sand cores, so as to improve design efficiency and production. Efficiency, improve process yield, reduce the effect of seam area
- Summary
- Abstract
- Description
- Claims
- Application Information
AI Technical Summary
Problems solved by technology
Method used
Image
Examples
Embodiment Construction
[0030] In order to illustrate the technical solution of the present invention more clearly, it will be described in detail according to the embodiments of the accompanying drawings. Obviously, the accompanying drawings in the following description are some embodiments of the present invention. For those of ordinary skill in the art, without paying Under the premise of creative work, other drawings can also be obtained based on these drawings.
[0031] The length of the T-shaped bed 1 involved in this embodiment is greater than 3m, and the volumes at both ends are unequal. According to the volume, it is divided into a large end and a small end. The T-shaped bed 1 is provided with a high guide rail and a low guide rail. This makes the T-shaped bed complex in the height direction. In the prior art, according to the structure of the T-shaped bed 1, the drainage groove structure in the sand core of the T-shaped bed is separately set up as an independent drainage groove sand core 4,...
PUM
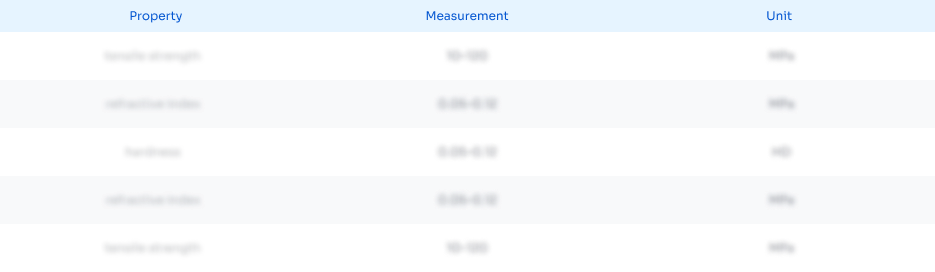
Abstract
Description
Claims
Application Information

- R&D Engineer
- R&D Manager
- IP Professional
- Industry Leading Data Capabilities
- Powerful AI technology
- Patent DNA Extraction
Browse by: Latest US Patents, China's latest patents, Technical Efficacy Thesaurus, Application Domain, Technology Topic, Popular Technical Reports.
© 2024 PatSnap. All rights reserved.Legal|Privacy policy|Modern Slavery Act Transparency Statement|Sitemap|About US| Contact US: help@patsnap.com