Casting method of mold core of casting mold
A casting mold and core technology, which is used in casting molding equipment, casting molds, cores, etc., can solve the problems of inability to pull cores, high manufacturing costs, and difficulty in dissolving, achieving abundant and renewable resources, and solving wax saponification. problems, the effect of improving the working environment
- Summary
- Abstract
- Description
- Claims
- Application Information
AI Technical Summary
Problems solved by technology
Method used
Examples
Embodiment Construction
[0012] (1) First, the mold is assembled and sealed, and liquid (water) is poured into the inlet, and then a sealing plug containing a drainage conduit is installed at the water injection port;
[0013] (2) Next, place the mold in an environment sealed with specified cooling and heat preservation effects and relatively airtight conditions; let it condense and form ice in the airtight environment;
[0014] (3) Then, the ice core obtained is taken out from the mould, and put into a designated environment to preserve for subsequent use;
[0015] (4) Finally, assemble the ice core into the mold, inject wax, cool, and melt the core to obtain the wax mold of the required cavity.
PUM
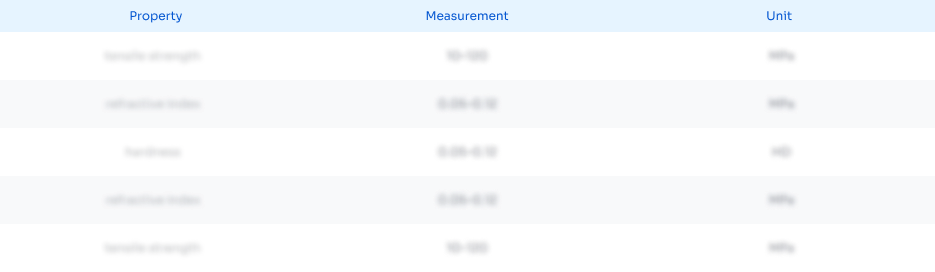
Abstract
Description
Claims
Application Information

- R&D
- Intellectual Property
- Life Sciences
- Materials
- Tech Scout
- Unparalleled Data Quality
- Higher Quality Content
- 60% Fewer Hallucinations
Browse by: Latest US Patents, China's latest patents, Technical Efficacy Thesaurus, Application Domain, Technology Topic, Popular Technical Reports.
© 2025 PatSnap. All rights reserved.Legal|Privacy policy|Modern Slavery Act Transparency Statement|Sitemap|About US| Contact US: help@patsnap.com