Space thin film structure clamp shape optimization design method for restraining creases
A space thin film, optimization design technology, applied in the direction of design optimization/simulation, calculation, special data processing applications, etc., can solve the problems that affect the shape accuracy and performance of the space structure, reduce the area of the thin film, out-of-plane buckling, etc., to achieve effective Facilitate assembly and space expansion, simple fixture configuration, and easy processing and manufacturing
- Summary
- Abstract
- Description
- Claims
- Application Information
AI Technical Summary
Problems solved by technology
Method used
Image
Examples
Embodiment Construction
[0025] Specific embodiments of the present invention will be described in detail below in conjunction with technical solutions and accompanying drawings.
[0026] In the first step, the shape optimization of the fixture components is performed
[0027] 1.1) Determine the design domain according to the size requirements of the structure and the actual loading situation, and divide the finite element element grid, and establish the finite element model of the membrane structure with clamps. Rigid fixture components were simulated with 1000 times the modulus of elasticity of the membrane. Select some design points on the connection line between the membrane and the fixture, and use B-spline function interpolation to generate the boundary of the fixture and the membrane. figure 1 is the design domain of the space film antenna structure, according to the symmetry of the structure, 11 design points are selected for each fixture, image 3 Design the domain for the solar sail struct...
PUM
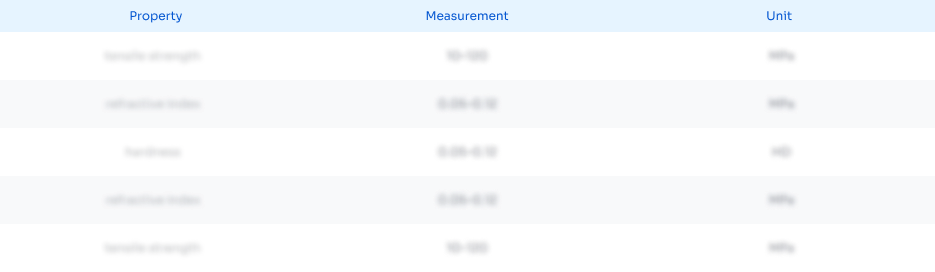
Abstract
Description
Claims
Application Information

- R&D
- Intellectual Property
- Life Sciences
- Materials
- Tech Scout
- Unparalleled Data Quality
- Higher Quality Content
- 60% Fewer Hallucinations
Browse by: Latest US Patents, China's latest patents, Technical Efficacy Thesaurus, Application Domain, Technology Topic, Popular Technical Reports.
© 2025 PatSnap. All rights reserved.Legal|Privacy policy|Modern Slavery Act Transparency Statement|Sitemap|About US| Contact US: help@patsnap.com