Method for separating halogenated olefin impurities from 2-chloro-1,1,1,2-tetrafluoropropane
A technology of halogenated olefins and tetrafluoropropane, which is applied in the field of separating halogenated olefins impurities, can solve the problems of activated carbon surface pulverization, reduced service life, and large impact of activated carbon, etc., and achieves the effect of large saturated adsorption capacity
- Summary
- Abstract
- Description
- Claims
- Application Information
AI Technical Summary
Problems solved by technology
Method used
Image
Examples
Embodiment 1-5
[0024] The preparation steps of embodiment 1-5 are as follows:
[0025] At 150° C., 1000 g of the adsorbent copper-modified high-silicon ZSM-5 molecular sieve was dried for 3 hours for later use. 100g of dried adsorbent is filled in the adsorption column of DN25mm×1000mm, and the composition containing 96.62% HCFC-244bb, 1.85% HCFO-1233xf, 0.12% HF and other halogenated olefins is continuously fed in the form of steam from the bottom of the adsorption column 100g, the material was recovered after 6 adsorption cycles, and the components were detected.
[0026] The preparation method of copper-modified high-silicon ZSM-5 molecular sieve is as follows: prepare saturated copper chloride solution at 60°C, add high-silicon ZSM-5 molecular sieve adsorbent into the reaction kettle, heat up to 60°C, and pump the vacuum to the reaction kettle Add an excess of saturated cupric chloride solution at 60°C; after immersion for 10 hours, filter and dry the molecular sieve to obtain the finis...
Embodiment 6-11
[0029] At 150° C., 1000 g of the adsorbent copper-modified high-silicon ZSM-5 molecular sieve was dried for 3 hours for later use. 100g of dried adsorbent is filled in the adsorption column of DN25mm×1000mm, and the excessive combination of 96.62% HCFC-244bb, 1.85% HCFO-1233xf, 0.12% HF and other halogenated olefins is continuously passed through from the bottom of the adsorption column in the form of steam until the adsorbent is saturated.
[0030] The preparation method of copper-modified high-silicon ZSM-5 molecular sieve is as follows: prepare saturated copper chloride solution at 60°C, add high-silicon ZSM-5 molecular sieve adsorbent into the reaction kettle, heat up to 60°C, and pump the vacuum to the reaction kettle Add an excess of saturated copper chloride solution at 60°C; after immersion for 13 hours, filter and dry the molecular sieve to obtain the finished product of copper-modified high-silicon ZSM-5 molecular sieve adsorbent.
[0031] See Table 2 for the raw ma...
Embodiment 12-15
[0033] After the adsorbent is saturated, heat the adsorption column to raise the temperature, and pass high-purity nitrogen that has been preheated to the same temperature as the adsorption column from the top of the adsorption column, and pass a certain amount of nitrogen to stop the desorption; the amount of nitrogen that is passed is 2000g.
[0034] See Table 3 for the temperature of the adsorption column in Examples 12-15 after heating and the related data of the adsorbent after desorption.
PUM
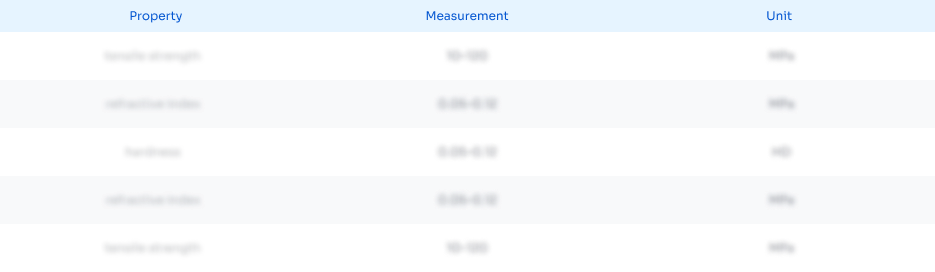
Abstract
Description
Claims
Application Information

- R&D Engineer
- R&D Manager
- IP Professional
- Industry Leading Data Capabilities
- Powerful AI technology
- Patent DNA Extraction
Browse by: Latest US Patents, China's latest patents, Technical Efficacy Thesaurus, Application Domain, Technology Topic, Popular Technical Reports.
© 2024 PatSnap. All rights reserved.Legal|Privacy policy|Modern Slavery Act Transparency Statement|Sitemap|About US| Contact US: help@patsnap.com