Electric power brake system with arbitrarily decoupled degrees of freedom for electric vehicles
A technology of electric power assist and electric vehicles, applied in the direction of brakes, brake transmission devices, vehicle components, etc., can solve the problems of single decoupling, complex power assist assembly mechanism, poor pedal feel retention, etc., and achieve simple mechanism structure , Wide adaptability of hardware equipment, and the effect of improving driving safety
- Summary
- Abstract
- Description
- Claims
- Application Information
AI Technical Summary
Problems solved by technology
Method used
Image
Examples
Embodiment Construction
[0035] An electric power-assisted braking system suitable for electric vehicles with any decoupling degree of freedom, including: brake pedal assembly 1, electric power assist assembly 2, liquid storage tank 3, brake master cylinder 4, decoupling device assembly 5. HCU 6, wheel cylinder 7, electronic control unit 8, booster motor assembly 9.
[0036] An electric power-assisted braking system suitable for electric vehicles with any degree of decoupling freedom, the brake pedal assembly 1 includes a brake pedal 101 , a pedal stroke sensor 102 , a pedal push rod 103 and a pedal shaft support 104 . The direction in which the pedal force of the brake pedal 101 is input is defined as the front. The top of the brake pedal 101 is connected to the rotating shaft bracket 104 through a hinge, and the pedal travel sensor 102 is also installed at the joint between the brake pedal 101 and the rotating shaft bracket 104 . The front end of the pedal push rod 103 is connected with the middle ...
PUM
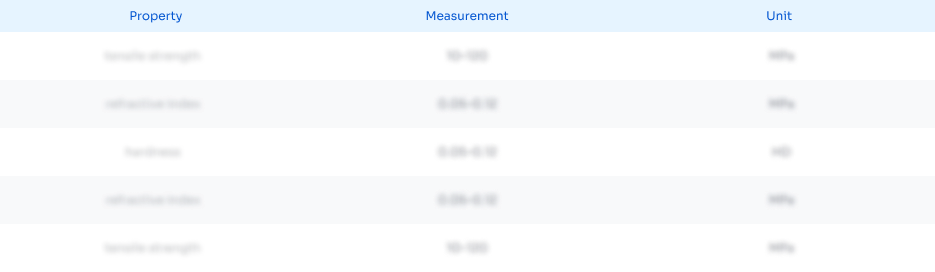
Abstract
Description
Claims
Application Information

- Generate Ideas
- Intellectual Property
- Life Sciences
- Materials
- Tech Scout
- Unparalleled Data Quality
- Higher Quality Content
- 60% Fewer Hallucinations
Browse by: Latest US Patents, China's latest patents, Technical Efficacy Thesaurus, Application Domain, Technology Topic, Popular Technical Reports.
© 2025 PatSnap. All rights reserved.Legal|Privacy policy|Modern Slavery Act Transparency Statement|Sitemap|About US| Contact US: help@patsnap.com