Method for detecting early fault of bearing through secondary phase coupling and improved bi-spectrum algorithm
A technology of secondary phase and detection method, applied in the direction of mechanical bearing testing, etc., can solve the problems of difficult fault characteristics, nonlinearity, low signal-to-noise ratio, etc., achieve stable and reliable detection ability, avoid bearing accidents, and have a wide range of applications.
- Summary
- Abstract
- Description
- Claims
- Application Information
AI Technical Summary
Problems solved by technology
Method used
Image
Examples
Embodiment 1
[0090] Example 1: Early fault detection of inner ring of 6205-2RS JEM SKF deep groove ball bearing
[0091] Bearing structure parameters: roller diameter D B =7.94mm; Bearing pitch diameter D P =39.04mm; Number of rollers N B =9. The diameter of a single defect in the inner ring of the bearing is 0.1778mm, and the depth of the defect is 0.2794mm.
[0092] Bearing operating environment: motor load 2HP, speed 1748r / min (29.1333Hz).
[0093] Data acquisition parameters: rotational speed and sampling frequency F of the vibration accelerometer signal on the bearing seat s =12000Hz, acquisition length N=122136.
[0094] According to these parameters and the structural parameters of the bearing, the theoretically calculated characteristic frequency of the inner ring defect of the bearing is F IRF =157.7628Hz, in the improved bispectral model algorithm of secondary phase coupling detection, the length of FFT analysis data is taken as 4096, and the frequency resolution is df=F s...
Embodiment 2
[0098] Example 2: Early fault detection of 6205-2RS JEM SKF deep groove ball bearing outer ring
[0099] Bearing structure parameters: roller diameter D B =7.94mm; Bearing pitch diameter D P =39.04mm; Number of rollers N B =9. The diameter of a single-point defect on the outer ring of the bearing is about 0.1778mm, and the depth of the defect is about 0.2794mm.
[0100] Bearing operating environment: motor load 2HP, speed 1750r / min (29.1667Hz).
[0101] Data acquisition parameters: rotational speed and sampling frequency F of the vibration accelerometer signal on the bearing seat s =12000Hz, acquisition length N=122136.
[0102] Based on these parameters and the structural parameters of the bearing, the theoretically calculated characteristic frequency of the bearing outer ring defect is F ORF =104.5567Hz, in the improved bispectral model algorithm of secondary phase coupling detection, the length of FFT analysis data is taken as 4096, and the frequency resolution is df=...
Embodiment 3
[0106] Example 3: MB ER-10K Bearing Roller Fault Detection
[0107] Bearing structure parameters: roller diameter D B =7.9248mm; bearing pitch diameter D P =33.4772mm; Number of rollers N B =8.
[0108] Bearing operating environment: speed 1807r / min (30.12Hz).
[0109] Data acquisition parameters: rotational speed and sampling frequency F of the vibration accelerometer signal on the bearing seat s =25600Hz, acquisition length N=472000.
[0110] According to these parameters and the structural parameters of the bearing, the theoretically calculated characteristic frequency of the bearing roller defect is F BF =119.9981Hz, in the improved bispectral model algorithm of secondary phase coupling detection, the length of FFT analysis data is taken as 4096, and the frequency resolution is df=F s / 4096=25600 / 4096=6.25Hz, the frequency resolution is too large, but the characteristic frequency of the bearing roller defect visible in the actual analysis is F RBF =floor(F BF / df)×...
PUM
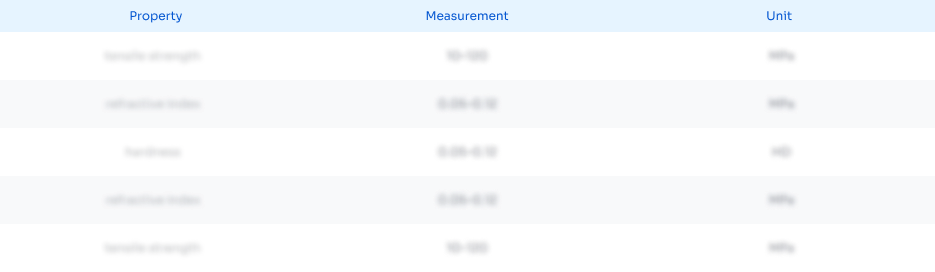
Abstract
Description
Claims
Application Information

- R&D Engineer
- R&D Manager
- IP Professional
- Industry Leading Data Capabilities
- Powerful AI technology
- Patent DNA Extraction
Browse by: Latest US Patents, China's latest patents, Technical Efficacy Thesaurus, Application Domain, Technology Topic, Popular Technical Reports.
© 2024 PatSnap. All rights reserved.Legal|Privacy policy|Modern Slavery Act Transparency Statement|Sitemap|About US| Contact US: help@patsnap.com