Design method of fabricated frame joint of H-shaped steel column and I-shaped beam horizontal pushing type dovetail tenon
A design method and technology of H-beams, which are applied in construction, building structure, processing of building materials, etc., can solve the problems of difficult connection of beam-column joints, difficult replacement or reuse of components, etc. Simple design and low cost
- Summary
- Abstract
- Description
- Claims
- Application Information
AI Technical Summary
Problems solved by technology
Method used
Image
Examples
Embodiment Construction
[0030] In order to better understand the technical content and installation process of the present invention, it is introduced in conjunction with the description of the drawings.
[0031] Step 1. The frame beams and columns are prefabricated in the factory, and the connecting components are prefabricated.
[0032] 1.1. The upper and lower flanges 54 of the beam end of the frame are doubled by flaring to form a dovetail 52, which is used to connect and anastomose the shoulder of the beam, such as figure 1 , 2 Shown. There are several reference methods for eversion measures: welding a piece of equal-width and equal-thickness iron plate at the end of the normal I-beam; cutting the flange at the position of the tenon at the beam end web, and welding a dovetail steel plate twice the thickness of the beam flange ; Take the binding method to process the dovetail 52 shape.
[0033] 1.2. The node area of the column end (direction of the strong axis connection beam) must be prefabricated w...
PUM
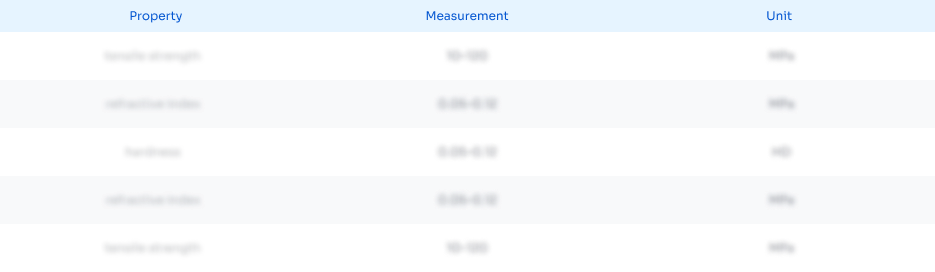
Abstract
Description
Claims
Application Information

- R&D Engineer
- R&D Manager
- IP Professional
- Industry Leading Data Capabilities
- Powerful AI technology
- Patent DNA Extraction
Browse by: Latest US Patents, China's latest patents, Technical Efficacy Thesaurus, Application Domain, Technology Topic, Popular Technical Reports.
© 2024 PatSnap. All rights reserved.Legal|Privacy policy|Modern Slavery Act Transparency Statement|Sitemap|About US| Contact US: help@patsnap.com