Method for preparing no-solvent green styrene-series cation exchange resin
A cation exchange and styrene-based technology, which is applied in the field of preparation of green styrene-based cation-exchange resins, can solve health hazards and other problems, achieve the effects of reducing pollution, not easy to break, and increasing skeleton elasticity
- Summary
- Abstract
- Description
- Claims
- Application Information
AI Technical Summary
Problems solved by technology
Method used
Examples
Embodiment 1
[0049] Add 250g of deionized water, 4g of anhydrous sodium sulfate, and 0.5g of polyvinyl alcohol into a three-necked flask to configure water phase A, then add 100g of styrene, 6g of divinylbenzene, 1g of initiator, and three The oil phase A prepared with 0.5 g of methylolpropane tris(3-mercaptopropionate) was stirred, heated up to polymerize, and then kept at a temperature of 4 hours, and a white ball was washed and dried. Add 120g of deionized water, 1.5g of anhydrous sodium sulfate, and 0.2g of polyvinyl alcohol into the three-necked flask to configure the water phase B, add a polywhite ball, heat up to 32°C and stir, then add 25g of styrene, divinylbenzene 1 g, 0.2 g of trimethylolpropane tris(3-mercaptopropionate) is configured as oil phase B, which is swelled for two hours, and the water phase is separated. Finally, add water phase C prepared by 300g deionized water and 0.5g polyvinyl alcohol, gradually heat up, keep warm for 8 hours after polymerization, and separate t...
Embodiment 2
[0053] Add 250g of deionized water, 4g of anhydrous sodium sulfate, and 0.5g of polyvinyl alcohol into a three-necked flask to configure water phase A, then add 100g of styrene, 6.8g of divinylbenzene, 1g of initiator, and two The oil phase A prepared with 0.8 g of ethylene glycol methacrylate was stirred, heated up to polymerize, and then kept warm for 4 hours, and a poly white ball was washed and dried. Add 120g of deionized water, 1.5g of anhydrous sodium sulfate, and 0.2g of polyvinyl alcohol into the three-necked flask to configure the water phase B, add a polywhite ball and raise the temperature to 32°C and stir, then add 25g of styrene and 2g of divinylbenzene , 0.5 g of ethylene glycol dimethacrylate was configured as oil phase B, which was swelled for two hours, and the water phase was separated. Finally, add water phase C prepared by 300g deionized water and 0.5g polyvinyl alcohol, gradually heat up, keep warm for 8 hours after polymerization, and separate the water ...
Embodiment 3
[0057] Add 250g of deionized water, 4g of anhydrous sodium sulfate, and 0.5g of polyvinyl alcohol into a three-necked flask to configure water phase A, and then add 100g of styrene, 7g of divinylbenzene, 1g of initiator, and ethylene glycol to the water phase. The oil phase A prepared with 1 g of alcohol diethyl diallyl ester was stirred, heated up to polymerize, and then kept warm for 4 hours, and a poly white ball was washed and dried. Add 120g of deionized water, 1.5g of anhydrous sodium sulfate, and 0.2g of polyvinyl alcohol into the three-necked flask to configure the water phase B, add a polywhite ball and raise the temperature to 32°C to stir, then add 25g of styrene, 1.2g of divinylbenzene g, 0.5 g of ethylene glycol diethyl diallyl ester is configured as oil phase B, which is swollen for two hours, and the water phase is separated. Finally, add water phase C prepared by 300g deionized water and 0.5g polyvinyl alcohol, gradually heat up, keep warm for 8 hours after pol...
PUM
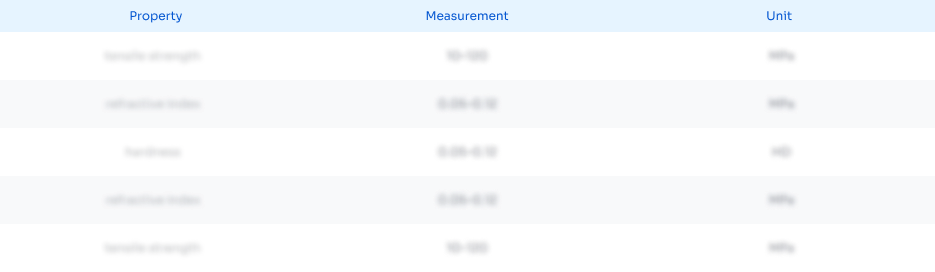
Abstract
Description
Claims
Application Information

- R&D
- Intellectual Property
- Life Sciences
- Materials
- Tech Scout
- Unparalleled Data Quality
- Higher Quality Content
- 60% Fewer Hallucinations
Browse by: Latest US Patents, China's latest patents, Technical Efficacy Thesaurus, Application Domain, Technology Topic, Popular Technical Reports.
© 2025 PatSnap. All rights reserved.Legal|Privacy policy|Modern Slavery Act Transparency Statement|Sitemap|About US| Contact US: help@patsnap.com